А. И. РОДИН
ПАЙКА СЕРЕБРЯНЫМИ ПРИПОЯМИ В ПЛАМЕНИ ГАЗОВОЙ ГОРЕЛКИ
ОБОРОНГИЗ 1954
Часть 1
ГОСУДАРСТВЕННОЕ ИЗДАТЕЛЬСТВО ОБОРОННОЙ ПРОМЫШЛЕННОСТИ Москва 1954ПАЙКА СЕРЕБРЯНЫМИ ПРИПОЯМИ В ПЛАМЕНИ ГАЗОВОЙ ГОРЕЛКИ
ОБОРОНГИЗ 1954
Часть 1
В брошюре описан передовой опыт пайки серебряными припоями газовой горелкой в приборостроении.
В ней рассматриваются стандартные серебряные припои, некоторые промежуточные припои, флюсы и несколько простейших приспособлений для пайки.
В книге приводится ряд примеров пайки отдельных деталей игузлов.
Брошюра рассчитана на рабочих-паялыциков и технологов, работающих в области пайки.
ВВЕДЕНИЕ
Пайка припоями занимает важное место в технологии точного приборостроения. Она дает надежные по прочности соединения различных металлов и сплавов и в настоящее время ею нередко заменяют сварку.
К преимуществам пайки припоями следует отнести отсутствие плавления и незначительный нагрев основного металла, что позволяет во многих случаях сохранить неизменными его химический состав, структуру и механические свойства; чистоту соединения; сохранение формы изделия, а также дешевизну и простоту процесса пайки.
Особенно широко применяется в приборостроении твердая пайка или пайка серебряными припоями, которые представляют собой тугоплавкие припои с содержанием серебра от 10 до 75%. Такие припои имеют незначительную разность потенциалов с латунью и бронзой, и шов, спаянный серебряными припоями, устойчив против коррозии и дает сравнительно прочное соединение. Эти качества серебряных припоев выделяют их среди других припоев, употребляемых при производстве приборов.
При правильном ведении пайки расход припоя незначителен. Оптимальная толщина его слоя в соединении составляет всего
0,03—0,08 мм.
В настоящей работе рассматривается пайка серебряными припоями с использованием для пайки пламени газовой горелки. Этот способ требует повышенного внимания и некоторых специальных навыков при ответственной пайке точных узлов из латуни и томпака.
ПРИПОИ И ФЛЮСЫ Стандартные серебряные припои
Серебряные припои — это обычно сплавы из серебра, меди и цинка. Они ковки и вязки и во многих‘случаях швы из них оказываются настолько же прочными, как и спаиваемые металлы.
В табл. 1 приведены состав и свойства серебряных припоев, применяемых в настоящее время в приборостроении.
Таблица 1 состав и свойства серебряных припоев

Пр имечания. 1. Серебряные припои поставляются по весу в виде зерен размером от 1 до 3 мм для припоев марок ПСр-10; ПСр-12 и ПСр-25 и в виде полос и прутков с размерами, указанными в заказе, для остальных марок.
2. Химический состав припоев дан согласно ОСТ 2982.
Припой ПСр-10 содержит 10% серебра — практически наименьшее количество в припое для твердой пайки. Он может служить для соединения деталей из стали и цветных сплавов, нагревающихся при
* Ориентировочные данные
работе до температуры 800° С, как, например, для пайки примусных горелок. Его применение целесообразно, когда детали в последующем подвергаются термообработке при сравнительно высоких температурах, не превышающих, однако, температуры плавления припоя. Припой ПСр-12 применяют для пайки латуней с содержанием меди 58п/о и более.
Для тонких работ, когда требуется особая чистота места спая, применяют припой ПСр-25. Однако шов из ПСр-25 плохо выдерживает ударные нагрузки и при стыковых соединениях дает трещины. Поэтому стыки деталей толщиной до 3 мм надежнее соединять припоем ПСр-45, который содержит значительно больше серебра, чем предыдущие. Он может быть использован для пайки деталей из меди, бронз, стали и никеля. Этот припой желтоватого цвета, вязок, жидкотекуч, хорошо сопротивляется коррозии. Шов из него хорошо выдерживает удары и вибрации.
Припой ПСр-65 применяют для пайки ленточных пил, а ПСр-70— для пайки проводов в тех случаях, когда важно, чтобы места спая не уменьшали резко электропроводность.
Заводы-изготовители обычно поставляют серебряный припой в виде листов, которые затем разрезают на полоски требуемой величины. Полученный путем сплавления кусок припоя прокатывают на вальцах до толщины листа 1,5—2 мм (или тоньше — в зависимости от метода пайки), а затем разрезают на полоски. Крайние (более широкие) полосы с неровными краями, получившимися при прокатке листа, используют при пайке крупных деталей (с длинным швом), где нужно много припоя.
Оставшиеся после пайки короткие прутки, которые уже нельзя держать руками, подпаивают к другим пруткам или на латунную проволоку с тем, чтобы использовать их до конца.
Для соединения мелких тонких деталей, требующих небольшого количества припоя, рекомендуется применять полоски шириной
0,5—3 мм.
> Промежуточные припои для специальных работ
При пайке сложных узлов и деталей в точном приборостроении чаще всего пользуются серебряными припоями, указанными в табл. 1.
Следует отметить, однако, что в последнее время эти серебряные припои не в полной мере удовлетворяют требованиям производства. В сложных по конструкции узлах требуется ступенчатая твердая пайка, которую при использовании газовой горелки нельзя производить одним припоем, так как запаянные ранее узлы вследствие близкого расположения швов друг от друга распаиваются при нагревании. Поэтому появилась потребность в промежуточном припое, который имел бы температуру плавления 500—600° С. Та-кой припой был разработан и получен в лабораторных условиях и при испытании дал хорошие результаты. Пайка узлов значительно облегчилась. Состав нового припоя следующий:
серебра .... ЗО% цинка..........16,7%
меди............20% кадмия .... 33,3%
Температура плавления 500—560° С. Применяется этот припой только для пайки изделий, не подвергающихся вибрациям, так как он хрупок.меди............20% кадмия .... 33,3%
При тщательной рихтовке длинных труб после пайки их припоем ПСр-45 в местах пайки по шву получались трещины. Чтобы не
допустить возникновения трещин, был разработан другой специальный припой следующего состава:
серебра ..........52%
меди ........ 28%
цинка . ........ 20%
меди ........ 28%
цинка . ........ 20%
Этот припой очень жидкотекуч; швы, спаянные им, выдерживают неоднократные вибрационные нагрузки. Он хорошо зарекомендовал себя при сложных пайках с последующими рихтовальными работами вблизи швов.
Приготовление флюсов
Большое значение для пайки металлов имеют флюсы. Флюс очищает соединяемые поверхности от грязи, растворяет или восстанавливает окисные пленки на них, защищает металл от окисления во время пайки. Другое важное назначение флюсов — понизить поверхностное натяжение в жидком металле (расплавленном припое). Увеличение под влиянием флюсов жидкотекучести припоя и смачиваемости металла припоем значительно улучшает качество пайки. Флюсы нужно подбирать таким образом, чтобы они не оказывали вредного химического воздействия на поверхность металла и не растворялись в нем.
В приводимой ниже табл. 2 * указаны важные для пайки физические свойства некоторых флюсов.

* Таблица заимствована из книги Г. И. Погодина-Алексеева «Теория сварочных процессов», Машгиз, 1945
При пайке с помощью газовой горелки в качестве флюса обычно применялась прокаленная бура, которая вводилась в место спая в виде порошка. Однако этому флюсу присущ серьезный недостаток: имея высокую температуру плавления, он долго сохраняет порошкообразное состояние и поэтому легко сдувается с соединяемых поверхностей пламенем газовой горелки, в результате чего появляется необходимость дополнительной обработки поверхности деталей и мест спая.
Чтобы флюс оставался на спаиваемой поверхности, буру кипятят в воде, затем кистью наносят полученный раствор на места соединения и дают ему высохнуть. На поверхности остается плотно прилегающий к металлу белый слой буры, который не дает окисляться ранее зачищенным местам пайки.
Однако при пайке мелких деталей, требующих высокой точности, паяльщики неохотно пользуются этим флюсом, так как высокая температура плавления буры усложняет работу. Так, например, при пайке припоем ПСр-45, имеющим более низкую температуру плавления, чем бура, может произойти зашлакование флюса.
В результате многочисленных опытов в настоящее время разработан и применяется флюс в виде жидкой пасты, замешенной на воде или спирте (лучше на спирте), который имеет следующий состав:
буры........................50 %
борной кислоты .......35%
фтористого калия.....15%
Технология приготовления флюса такова:борной кислоты .......35%
фтористого калия.....15%
1) обезводить фтористый калий на противне из нержавеющей стали при температуре 250° С в течение 4—5 час.;
2) отвесить компоненты флюса согласно рецептуре, тщательно перемешать их и расплавить;
3) размешать расплавленный флйс фарфоровым или стальным стержнем и вылить на стальную плиту;
4) разбить флюс на куски и размолоть в фарфоровой шаровой мельнице до состояния пудры;
5) просеять через сито № 0,25—0,14 и собрать в стеклянную банку с притертой или резиновой пробкой, так как флюс гигроскопичен.
Использование этого флюса дает неплохие результаты.
При нагреве примерно до 600° С флюс расплавляется, образуя очищенное место для припоя. Припой не растекается по всей поверхности, а остается только там, где был раньше нанесен слой флюса. Чем ровней и аккуратней будет нанесен флюс на спаиваемую поверхность, тем больше межно сэкономить припоя.
Для пайки деталей, у которых при зачистке торцевых соединений в местах заполнения зазоров по шву не должно быть в припое никаких раковин, применяется специальный флюс, состоящий из равных частей тетрафторбората калия, фтористого калия и борной кислоты.
Необходимый для приготовления этого флюса тетрафторборат калия приготовляют двумя способами.
Способ I. В платиновую чашку помещают фтористый калий и растворяют в 20%-ной плавиковой кислоте.
При этом протекает реакция
KF+HF=KHF2.
Расчет необходимого количества данных компонентов производится по молекулярному весу в соответствии с реакцией. По растворении фтористого калия полученный раствор выпаривают на песчаной бане до образования кристаллов калия фтористого кислого (KHF2), которые вместе с раствором охлаждают. Затем кристаллы отделяют от раствора при помощи воронки Бюхнера, промывают их
2—3 раза спиртом и сушат.
После этого приготовляют концентрированный раствор борной кислоты, который помещают в платиновую чашку, и при помешивании прибавляют к нему ранее полученную сухую соль калия фтористого кислого.
При этом протекает следующая реакция:
2KHF2+Н3ВО3=KBF4+КОН+2Н2О.
Расчет необходимого количества данных компонентов производится по молекулярному весу в соответствии с реакцией. Полученный раствор выпаривают на песчаной бане до образования осадка тетра-фторбората калия (KBF4), который вместе с раствором охлаждают, а затем отделяют от раствора при помощи воронки Бюхнера, промывают несколько раз дистиллированной водой и сушат в сушильном шкафу при температуре 100ЭС в течение 45—60 мин.
Способ II. В платиновой чашке или в стеклянном стакане, покрытом внутри парафином, растворяют борную кислоту в 20%-ном растворе плавиковой кислоты до получения насыщенного раствора.
При этом протекает реакций
Н3ВО3+4HF=HB F4+ЗН2О.
Процесс насыщения ведут при комнатной температуре, для чего чашку или стакан охлаждают холодной водой. К полученному раствору борфтористой кислоты добавляют насыщенный при нагревании раствор КСl или KN03 или К2СО3 до прекращения выделения осадка тетрафторбората калия. При этом протекает следующая реакция:
HBF4+КС1=KBF4+HCI.
Осадок тетрафторбората калия отсасывают при помощи воронки Бюхнера, промывают водой до тех пор, пока промывная жидкость не будет давать реакцию (при помощи азотнокислого серебра) на ион хлора, и сушат в сушильном шкафу при 100° С в течение 45— 60 мин.
Описанный флюс с тетрафторборатом калия имеет существенный недостаток — он не ложится на горячие детали. Поэтому подготовку
к пайке приходится вести с заранее зафлюсованными и еще холодными деталями;
Другой недостаток этого флюса состоит в том, что он широко расплывается от шва по наружной поверхности, а это ведет к излишнему расходу припоя.
Для пайки ответственных узлов, требующих чистоты и полного пропая шва, применяется также флюс, состоящий из:
тетрафторбората калия ....................70%
буры .................... .................... .... 30%
буры .................... .................... .... 30%
Этот флюс дает неплохие результаты и относительно прост в изготовлении.
ПОДГОТОВКА К ПАЙКЕ
Соединяемые поверхности перед пайкой должны быть очищены от грязи, жира, окислов, следов смазки и охлаждающих жидкостей, применяемых при механической обработке.
Загрязнения, окисная пленка и пр. удаляются с поверхностей химическим или механическим путем.
Химическим способом — производится обезжиривание и травление в кислотах, после которого детали должны быть хорошо промыты и просушены.
Механическим способом — сначала поверхности тщательно протираются тряпкой (концами). После этого тонким наждачным полотном (шкуркой) № 180—240 зачищают места спайки деталей. Можно также применять для зачистки напильники.
Обычно применяют очистку механическим способом. Химическим способом обрабатывают детали, имеющие сложные рельефы и поэтому трудоемкие при механической очистке.
При сборке узлов и подготовке их под пайку применяется предварительное нанесение флюса на сопрягаемые поверхности.
Собранные детали должны быть достаточно прочно скреплены, для чего их прижимают струбцинами, скрепляют проволокой, ставят на шпильки или применяют технологические резьбовые отверстия в соединяемых деталях, или же используют специальные приспособления для устранения возможности смещения деталей при нагреве в процессе пайки.
Поверхность детали, которая не принимает участия в пайке, и особенно поверхность приспособления, применяемого при пайке, покрываются при сборке пастой из мела или графита (или их смеси) , крокуса, замешенного на воде, устраняющих смачивание поверхности припоем.
При нормальном процессе пайки соединение осуществляется тонким слоем припоя, который всасывается в малый зазор между кромками. Источник тепла не действует непосредственно на кромки, и они нагреваются постепенно, благодаря теплопроводности основного металла.
ПРИМЕНЕНИЕ ПРИСПОСОБЛЕНИЙ И ОПРАВОК
Существует ряд простых и дешевых приспособлений и оправок, которые значительно облегчают ведение пайки.
Очень важным является принятие всех мер, направленных на уменьшение потерь тепла. Нежелательно проводить пайку непосредственно на металлических столах и т. п., хорошо проводящих тепло В таких случаях под деталь, подвергаемую пайке, обычно подкладывают асбестовый лист. Вокруг деталей, подвергающихся пайке, рекомендуется устанавливать экраны из огнеупорных кирпичей или .листового асбеста.
Необходимость этого объясняется тем, что для пайки газовым пламенем температура пламени хотя и достаточна, но не столь высока, чтобы в короткое время доводить детали до нужной степени нагрева. Устройство экранов значительно сокращает общее время пайки.
Самым простым приспособлением для фиксации детали служат соответственным образом обработанные (засверленные, долбленные и прочие) огнеупорные кирпичи.
Иногда делают искусственную подстилку для мелких деталей, которая состоит из 65'% порошка угля и 35!% мелко истолченной ■огнеупорной глины. К смеси добавляют горячую кашицу, состоящую из 50 г рисовой муки на 250 см3 воды. В подстилку, помещенную в выемке камня или кирпича, вдавливают детали, затем вынимают их, сушат подстилку в печи, закладывают детали обратно и производят пайку.
Применение предварительной опрессовки, установки на шпильки или на крепление резьбовыми винтами и др. виды крепления значительно уменьшают количество приспособлений, необходимых для взаимного фиксирования деталей и узлов. Часто при подгонке деталей друг к другу пользуются струбцинами для удержания деталей в нужном положении, пайкой прихватывают их в нескольких местах (точках), а затем, освободившись от струбцин, производят пайку обычным образом.
ОБЩИЕ ТРЕБОВАНИЯ К КОНСТРУКЦИИ ПАЯНЫХ ДЕТАЛЕЙ
Паяные соединения — швы должны отвечать ряду требований. Шов должен быть прежде всего прочным. Механическая прочность мест спая имеет большое значение. Шов должен быть также плотным — обеспечивать герметичность соединения.
Электропроводность в местах спая токопроводящих деталей не должна понижаться.
Чтобы добиться высокого качества соединения, очень важно правильно выбрать припой.
При выборе припоя необходимо учитывать:
а) род металла, подвергаемого пайке;
б) необходимую прочность и плотность шва, определяемую условиями работы изделия;
в) конструктивные требования;
г) возможность проведения термической обработки деталей, имеющих паяные соединения, при температуре ниже точки плавления припоя.
Способ изготовления детали, способ соединения отдельных элементов в заготовку оказывает существенное влияние на конструктивные формы детали.
Конструкции деталей, которые предназначены для соединения методом пайки, должны отличаться от конструкций аналогичных деталей, рассчитанных на соединение сваркой, клепкой и т. п.

Фиг. 1 Пайка встык мед- Фиг. 2. Напайка на лист
ной проволоки. для усиления резьбы.
При конструировании паяных соединений нужно' помнить, что прочность шва непосредственно зависит от площади спая и взаимной подгонки соединяемых деталей (зазоры под пайку), поэтому швы при соединении внахлестку значительно прочнее, чем при соединении встык.
Пайку встык применяют для самых различных случаев. Приведем несколько примеров. Пайкой встык пользуются для соединения
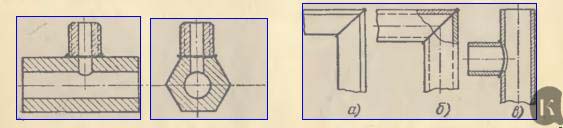
Фиг. 3. Пайка резьбовой втулки. Фиг. 4. Пайка угольников и труб.
а—пайка угольников; б и в—пайка труб.
концов тонкой медной проволоки (фиг. 1), которую имеется в виду впоследствии для изоляции обертывать или же покрывать слоем лака. Так же спаивается проволока, которая подвергается протяжке на меньшие диаметры.
Пайку встык применяют для спайки тонкого листа с усиливающей его деталью, имеющей внутреннюю нарезку (фиг. 2).
Точно так же встык спаивают детали, изготовление которых из целого куска металла невозможно или почему-либо неудобно. Так соединяют, например, резьбовую втулку с отверстием другой детали (фиг. 3).
Очень часто пайка встык применяется для соединения труб и угольников (фиг. 4). Пайка в данном случае представляет собой простой способ соединения при неточных и грубых работах. При пайке точных соединений часто требуется специальное приспособление или же после пайки необходимо производить механическую обработку и зачистку с рихтовкой в местах пайки.
При пайке к трубе 2 (фиг. 5) патрубков 1 раньше применялось соединение, показанное на фиг. 4, в. Отверстие в трубе было расточено по 3-му классу точности. После пайки получались большие коробления, несоосность патрубков; деталь часто попадала в брак. Было разработано другое соединение патрубков, показанное на фиг. 5. Отверстия в трубе были изготовлены с припуском под дальнейшую механическую обработку после пайки.
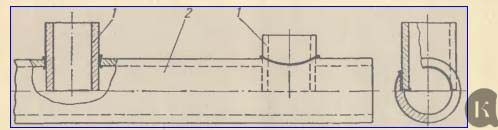
Фиг. 5. Пайка трубы с технологическим отверстием для патрубков. 1—патрубки; 2—труба.
Базовые отверстия под патрубки были расточены до половины трубы, как показано на фигуре. Во время пайки патрубки заранее устанавливались в правильное положение по оси трубы.
Припой проходил все места соединения и щели не оставалось.
После пайки технологический торец, выходящий внутрь трубы, фрезеровался до внутренней стенки трубы и затем растачивался до
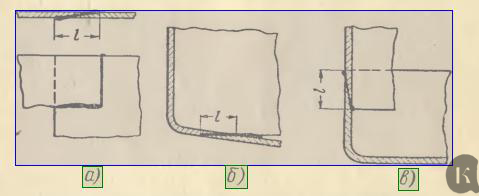
Фиг. 6. Пайка шва соединенными скошенными кромками.
необходимого размера. Такая конструкция соединения себя оправдала и может быть рекомендована при спайке труб и патрубков,, к которым применяются повышенные требования.
Образование шва пайкой встык применяется при изготовлении труб или колец, сгибаемых из листового материала. Такие кольца делаются обычно из листовой латуни толщиной примерно от 0,3 до 2 мм.
Пайкой встык пользуются также для соединения концов ленточных пил; чтобы избежать прожигания, части их нагревают раскаленными плитами.
На фиг. 6 показана пайка скошенными краями. Такая пайка применяется для соединения листов толщиной более 1 мм (см. фиг. 6, а).
По этому способу выполняют пайку больших медных резервуаров (фиг. 6, б и в).
Величина напуска I для листов разной толщины определяется по следующей таблице:

Паяные швы внапуск (фиг. 7) часто встречаются во многих изделиях при изготовлении тонкостенных сосудов, а именно — при соединении боковых стенок со вставными днищами. Толщина цилиндрической стенки берется больше толщины дна и крышки для того, чтобы изделие меньше коробилось при пайке.
При пайке деталей разных форм стремятся не приставлять одну деталь к другой в упор или встык, а выполняют конструкцию так, чтобы одна деталь входила в другую на некоторую глубину.
Это называется впаиванием. Впаивание позволяет разгрузить место пайки и облегчает правильное взаимное расположение соединяемых деталей при пайке.
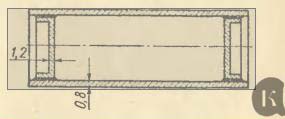
Фиг. 7. Пайка цилиндров, у которых швы внапуск.
На фиг. 8 показана пайка труб с фланцами. На фиг. 8, а фланец состоит из шайбы, толщина которой больше толщины стенки трубы ^для того чтобы во время пайки внутри не было кольцевых коробле-

Фиг. 8. Положение фланцев Фиг. 9. Соединение пайкой
на трубах при пайке. труб с резьбовыми втулками.
ний и утяжек). Если отверстие трубы изготовляется по 3-му или 4-му классу точности и должно иметь правильную геометрическую форму, то расточку следует производить после пайки.
На фиг. 8, б фланец выдавлен из тонкого листового материала с более широкой плоскостью опоры.
^Соединение пайкой труб со втулками (фиг. 9) с заранее нарезанной резьбой и расточенным отверстием рекомендуется производить, если не требуется большой точности в сопряжении осевых линий,
если же требуется получить точность до 4-го класса (а иногда и до 5'го), то нарезание резьбы рекомендуется производить после пайки.
Соединение пайкой труб с трубами рекомендуется производить, как указано на фиг. 10. Из этих комбинаций можно составить раз-

Фиг. 10. Виды возможных соединений труб пайкой.
личные соединения труб. Если нужно выдержать совпадение центровых линий, то необходимо оставлять припуски на расточку и на обточку их диаметров после пайки.
При изготовлении установочного винта из двух частей при плотной посадке шайбы на винт необходимо предусматривать в шайбе канавки шириной 0,2 мм и глубиной 0,3 мм (фиг. 11) для подведения припоя по всей плоскости канавки, особенно в случае, когда шайба окончательно обрабатывается после пайки. Нужно стремиться при изготовлении отдельных элементов паяных заготовок не допускать копирования сварочных соединений,
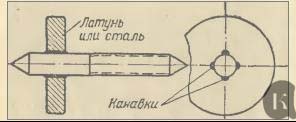
Фиг. 11. Технологические канавки для пайки соединения без зазоров
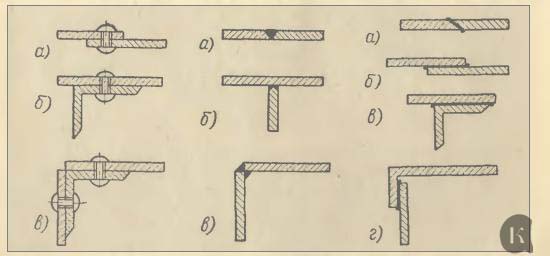
Фиг. 12. Виды заклепочных соединений.
Фиг. 13. Виды сварных соединений.
Фиг 14. Виды паяных соединений.
так как эти два вида соединения деталей совершение различны, что будет видно из дальнейшего.
Конструирование соединений с учетом технологии пайки позволяет получать высокую прочность этих соединений и экономически-выгодно.
На фиг. 12 и 13, заимствованных нами из работы В. Б. Гокуна, приведены примеры заклепочных и сварных соединений.
Конструкции паяных соединений таких же деталей показаны на фиг. 14.
В то время как предварительная механическая обработка кромок свариваемых элементов заготовки является неизбежной (фиг. 15, а), для паяных соединений (см. фиг. 15,6) обработки фасок не требуется.
Для сварки цилиндрических деталей производят разделку кромок, как показано' на фиг. 16, а. Для пайки же необходима совершенно другая конструкция присоединения дна (см. фиг. 16,6). Диаметр Б берется в размер, если это не требует особой точности изготовления, или же предварительно обработанный цилиндр берется;
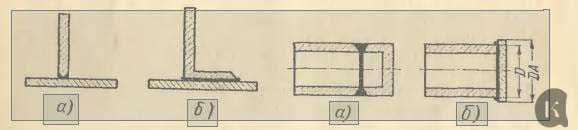
Фиг. 15. Конструкция аналогичного Фиг. 16. Конструкция аналогичного
соединения для сварки и пайки. соединения для сварки и пайки.
а—обработка кромок заготовки до сварки; а—обработка кромок заготовки до сварки;
б—для пайки конструкция должна быть без кромок. б—для пайки дна необходим припуск.
с припуском для окончательной обработки после пайки, а диаметр дна Оа берется больше диаметра самой заготовки еще на 1—6 мм, так, чтобы кромки дна выступали на 0,5—3 мм на сторону. Это» дает возможность производить пайку при вертикальном положении цилиндра. Такое положение удобно для пайки.
ПАЙКА ПЛАМЕНЕМ ГАЗОВОЙ ГОРЕЛКИ
Газовая пайка производится с помощью газовой горелки. Для пайки мелких деталей пользуются горелками, работающими на воздухе и светильном газе или ацетилене. Пламя светильного (саратовского) газа дает результаты лучшие, чем кислородно-ацетиленовое, а работа на светильном газе обходится значительно дешевле.
Газовые горелки применяются как специального типа для пайки (дают широкий факел пламени), так и обычные сварочные. Первые Дают менее концентрированный нагрев и охватывают сразу значительную поверхность. Пламя должно быть слегка окислительным, акое пламя дает прочный шов.
При пайке деталей небольшими партиями желательно производить предварительный подогрев деталей и приспособления в элек-тРошкафу. Это дает значительную экономию времени на рабочем
месте и обеспечивает равномерный подогрев всех деталей узла, а следовательно, позволяет избежать коробления и других дефектов при пайке тонких деталей.
Перед пайкой детали располагают на верстаке или в приспособлении так, чтобы их нужно было как можно меньше передвигать в процессе пайки.
Перед самой пайкой на деталь в местах спая наносится слой флюса. Если необходимо во время работы добавить флюс, то горячий конец прутка припоя погружают во флюс, и затем последний во время пайки попадает на соединяемые поверхности. Чтобы обеспечить равномерный нагрев деталей в местах спая, газовую горелку нужно все время передвигать.
При пайке разнородных сплавов пламя нужно направлять на тот из них, который является лучшим проводником тепла. При нагреве деталей различной толщины для достижения равномерного нагрева более толстые (массивные) части деталей необходимо прогревать в течение более продолжительного времени. Расплавление припоя нужно производить, касаясь им краев нагретых деталей. Если припой не пошел в месте спая, а пошел мимо шва, то очевидно детали еще нагреты неравномерно. Нельзя плавить припой в самом пламени горелки и допускать, чтобы он стекал каплями.
Пламя нужно держать перед местом пайки, так как припой затекает в более горячие места. Не следует прогревать места спая в течение слишком длительного времени, ибо это может привести к изменению состава припоя (к его выгоранию) и уменьшению эффективности действия флюса.
ПРАКТИЧЕСКИЕ ПРИМЕРЫ ПАЙКИ
Приведем ряд конкретных советов для разных случаев пайки деталей серебряными припоями.
1. Показанные на фиг. 17, г, д и е типы соединений листов и труб при пайке желательно не применять, заменяя их по возможности соединениями, показанными на фиг. 17, а, б и в. Во втором случае (а, б, в) легче получить качественный шов с наплывом в виде пояска, так как припой затекает между пригнанными друг к другу с зазорами деталями.
2. При конструировании паяных труб с фланцами необходимо учитывать и правильное положение фланцев на трубах для пайки. На фиг. 18, а показано правильное расположение (в двух случаях) фланцев на трубе под пайку. На фнг. 18, б показано расположение фланцев на трубе, которое применять не рекомендуется.
3. Не следует делать в местах спая фасок и закруглений (фиг. 19, а). Правильная конструкция показана на фиг. 19,6*.
4. При соединении, показанном на фиг. 20, лучше применять вариант б. В этом случае деформации, возникающие из-за внутренних напряжений, минимальны; такой вариант соединения более конструктивен, площадь спай увеличена (по сравнению с вариантом а) и, следовательно, прочность такого соединения выше.
5. Последовательность изготовления паяной заготовки, изображенной на фиг 21, а, осуществлена неправильно; нарезание резьбы в отверстии патрубка, а также окончательная обработка фланца
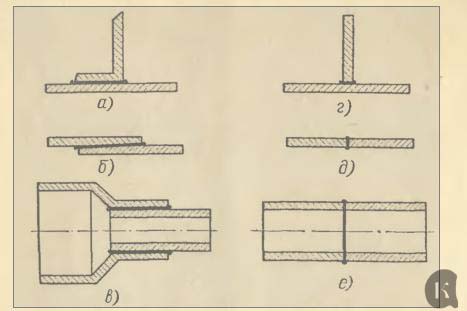
Фиг. 17. Типы соединения листов и труб.
а, б, в—удобные для пайки конструкции; г, д, е-~неудачные конструкции.
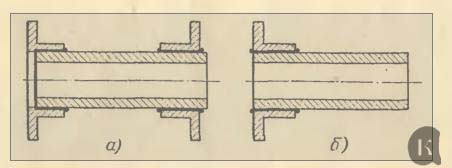
Фиг. 18. Соединение труб с фланцами а—правильное соединение для пайкн; б—неправильное соединение.
произведены до пайки этих деталей. Чтобы предотвратить коробление обработанных поверхностей в точных деталях, необходимо отделочные операции механической обработки выполнять после пайки. На фиг. 21,6 показаны соединяемые заготовки без окончательной механической обработки, и только после пайки соединенную деталь обрабатывают до вида, показанного на фиг. 21, а.
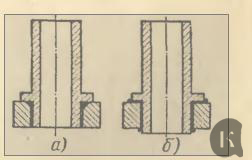
Фиг. 19. Паяное соединение.
а—неправильная конструкция; б— правильная конструкция
6. При конструировании нужно иметь в виду, что при очень плотных соединениях, например прессовых, и плотных посадках проход припоя внутрь в местах соединения невозможен. Узлы, имеющие герметичное сочленение, необходимо снабжать технологическим отверстием или прорезом для выхода расширяющегося при нагреве воздуха, так как в противном случае воздух препятствует затеканию
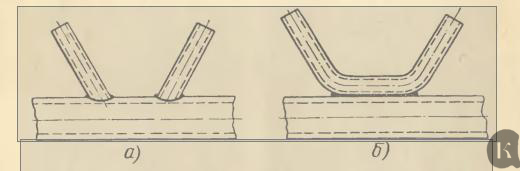
Фиг. 20. Деформации от внутренних напряжений при пайке.
а—конструкция, дающая максимальные деформации; б—конструкция, дающая минимальные деформации.
припоя (фиг. 22, а).
На фиг. 22,6 показано вентиляционное (технологическое) отверстие, которое впоследствии может также служить и отверстием под резьбу или отверстием для штифта, если по условиям конструкции это необходимо.
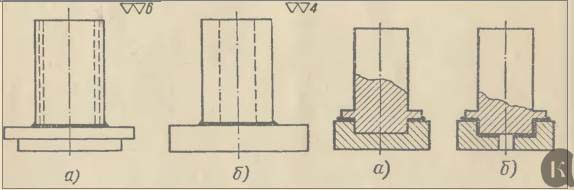
Фиг. 21. Последовательность Фиг. 22. Пайка узла с герметическим сочленением.
изготовления заготовки для пайки. а—неправильная конструкция;
а—неправильная; б—правильная. б—правильная конструкция.
7. Если при сварном соединении (фиг. 23, а) для окончательной обработки детали расстояние до1 шва должно' быть не менее 3 мм, чтобы последующей обработкой не ослабить сварного- шва, то при паяном соединении (см. фиг. 23,6) требуется всего 0,3—2 мм для выставки цилиндра за торец фланца под пайку. Этот припуск облегчает процесс пайки и создает удобные условия для затекания припоя в зазор. После пайки производят механическую обработку, которая обеспечивает получение чистого и правильного торца детали.
8. На фиг. 24,а показана конструкция соединения, в котором при сварке получается оплавление острых углов ребер. При паяном же соединении подобного типа (см. фиг. 24,6) этого явления не наблюдается. На острых углах такого соединения скопляется больше припоя, чем на плоскости.

Фиг. 23. Конструкция соединения фланца с трубой, с—для сварки; б—для пайки.
9. На фиг. 25,с и б показано соединение, в котором при изготовлении точных деталей рекомендуется производить механическую обработку после пайки. Если паять такие детали после окончательной обработки по 3-му классу точности, то при тонкостенных
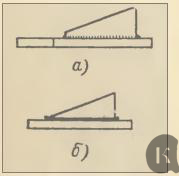
Фиг. 24. Конструкция аналогичного соединения для сварки и пайки.
а—конструкция для сварки; при сварке получается оплавление острых углов ребер; б—конструкция для пайки.
деталях (до 3 мм) получается коробление. Это ведет к браку или, в лучшем случае, вызывает дополнительную работу по исправлению деталей.
Вообще во- всех видах точных соединений лучше по возможности производить механическую обработку после пайки.
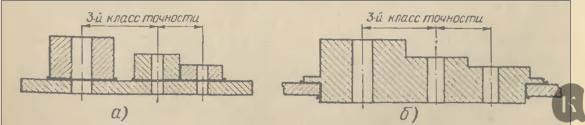
Фиг. 26. Соединение втулки с пластиной или трубой, а—неудачная конструкция; б—удачная конструкция.
Часть 2*
*в разработке