<1 часть Часть 3>*
*в разработке
А. И. РОДИН
ПАЙКА СЕРЕБРЯНЫМИ ПРИПОЯМИ В ПЛАМЕНИ ГАЗОВОЙ ГОРЕЛКИ
ОБОРОНГИЗ 1954
часть 2 *в разработке
ПАЙКА СЕРЕБРЯНЫМИ ПРИПОЯМИ В ПЛАМЕНИ ГАЗОВОЙ ГОРЕЛКИ
ОБОРОНГИЗ 1954
часть 2 *в разработке
10. На фиг. 26, а показан случай, когда втулки нужно припаять к пластине или трубе, выдержав координаты между центрами по
3-му классу точности. На практике в таких случаях обычно удается добиться только 4-го. класса точности. Изображенная конструкция не технологична. Более удачна конструкция, показанная на фиг. 26, б, где все отверстия сделаны в единой целой заготовке и остается только припаять ее в двух местах к пластине или трубе.
11. При пайке втулок к плоским деталям нужно производить соединение, как показано на фиг. 27, а, чтобы торец втулки выходил на 0,2—0,5 мм за плоскость припаиваемой детали. Другая конструкция (см. фиг. 27, б) применяется, если есть возможность подобрать
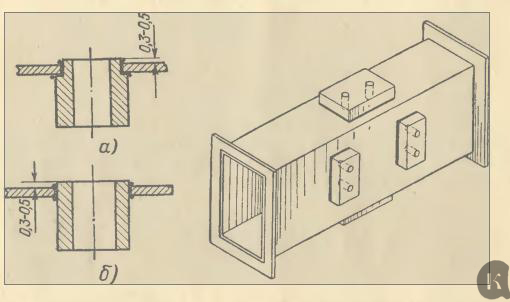
Фиг. 27. Виды соединения втулок с плоскими деталями. Фиг. 28. Крепление штифтами под пайку.
соответствующий размер трубы с учетом припуска на механическую обработку. В этом случае заточек в трубе не делают, а растачивают только отверстие в заготовке. Такой способ позволяет избежать затрат на излишнюю механическую обработку трубы.
12. На фиг. 28 показана пайка нескольких бобышек к трубе. Расположение бобышек в конструкции должно быть таким, чтобы можно было выполнить все пайки или большинство из них без изменения положения изделия. Нужно также предусмотреть крепление деталей под пайку на штифтах или шпильках. Это необходимо для фиксирования положения деталей во время пайки. Если нужно произвести несколько паек в непосредственной близости друг от друга, то следует предусмотреть применение припоев с различными температурами плавления, начиная с более тугоплавких и переходя к более легкоплавким. Разницу температур плавления между припоями при пайке необходимо принимать для обычных средних деталей 90— 100° С, для мелких деталей 120—150° С.
13. В примере, рассматриваемом на фиг. 29, требуется спаять втулку и стержень. На фиг. 29, а втулка вставляется в отверстие стержня, которое расточено по 4-му классу точности до половины диаметра стержня, с таким расчетом, чтобы во время пайки припой затек в зазор и припаял торец втулки к стержню. В этом случае конструкция разработана правильно. Втулка становится в центре стержня. В другом случае (см. фиг. 29, б) втулка устанавливается на окружность. Но центрировать ее при этом трудно и необходимы специальные приспособления для установки ее перпендикулярно оси
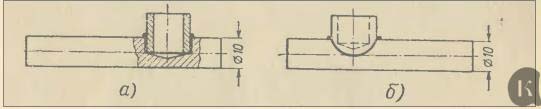
Фиг. 29. Соединение втулки со стержнем.
стержня. В случае, рассмотренном на фиг. 29, б, на стержне под втулкой после пайки возникает прогиб вследствие утяжки во1 время пайки. При диаметре стержня 10 мм он составляет 0,1—-0,3 мм. По условиям изготовления детали это недопустимо. Рихтовать также нельзя, так как во время рихтовки деталь ломается под втулкой.
Чтобы избежать прогиба, нужно дать технологический припуск по 1 мм на сторону (для диаметра 10 мм).
В конструкции, показанной на фиг. 29, а, после пайки прогиба нет совсем или же он незначителен и легко исправим.
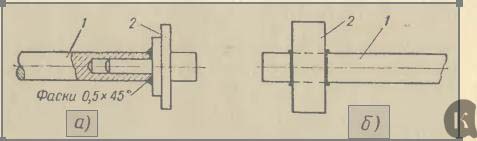
3-му классу точности. На практике в таких случаях обычно удается добиться только 4-го. класса точности. Изображенная конструкция не технологична. Более удачна конструкция, показанная на фиг. 26, б, где все отверстия сделаны в единой целой заготовке и остается только припаять ее в двух местах к пластине или трубе.
11. При пайке втулок к плоским деталям нужно производить соединение, как показано на фиг. 27, а, чтобы торец втулки выходил на 0,2—0,5 мм за плоскость припаиваемой детали. Другая конструкция (см. фиг. 27, б) применяется, если есть возможность подобрать
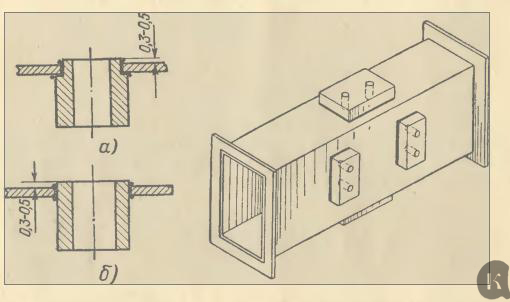
Фиг. 27. Виды соединения втулок с плоскими деталями. Фиг. 28. Крепление штифтами под пайку.
соответствующий размер трубы с учетом припуска на механическую обработку. В этом случае заточек в трубе не делают, а растачивают только отверстие в заготовке. Такой способ позволяет избежать затрат на излишнюю механическую обработку трубы.
12. На фиг. 28 показана пайка нескольких бобышек к трубе. Расположение бобышек в конструкции должно быть таким, чтобы можно было выполнить все пайки или большинство из них без изменения положения изделия. Нужно также предусмотреть крепление деталей под пайку на штифтах или шпильках. Это необходимо для фиксирования положения деталей во время пайки. Если нужно произвести несколько паек в непосредственной близости друг от друга, то следует предусмотреть применение припоев с различными температурами плавления, начиная с более тугоплавких и переходя к более легкоплавким. Разницу температур плавления между припоями при пайке необходимо принимать для обычных средних деталей 90— 100° С, для мелких деталей 120—150° С.
13. В примере, рассматриваемом на фиг. 29, требуется спаять втулку и стержень. На фиг. 29, а втулка вставляется в отверстие стержня, которое расточено по 4-му классу точности до половины диаметра стержня, с таким расчетом, чтобы во время пайки припой затек в зазор и припаял торец втулки к стержню. В этом случае конструкция разработана правильно. Втулка становится в центре стержня. В другом случае (см. фиг. 29, б) втулка устанавливается на окружность. Но центрировать ее при этом трудно и необходимы специальные приспособления для установки ее перпендикулярно оси
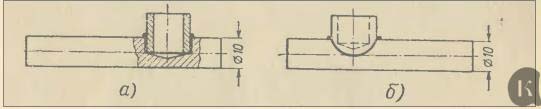
Фиг. 29. Соединение втулки со стержнем.
стержня. В случае, рассмотренном на фиг. 29, б, на стержне под втулкой после пайки возникает прогиб вследствие утяжки во1 время пайки. При диаметре стержня 10 мм он составляет 0,1—-0,3 мм. По условиям изготовления детали это недопустимо. Рихтовать также нельзя, так как во время рихтовки деталь ломается под втулкой.
Чтобы избежать прогиба, нужно дать технологический припуск по 1 мм на сторону (для диаметра 10 мм).
В конструкции, показанной на фиг. 29, а, после пайки прогиба нет совсем или же он незначителен и легко исправим.
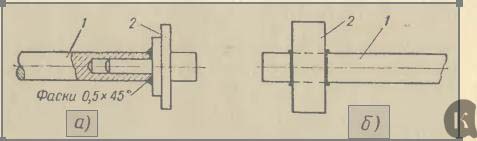
Фиг. 30. Паяное соединение двух деталей.
а—неправильная конструкция; б—правильная конструкция.
14. На фиг. 30, а показана неправильная конструкция двух спаиваемых деталей. В стержень / запрессовывается деталь 2, которая затем должна быть припаяна. Под пайку оставлена на детали фаска
0,5X45°.
По условиям работы соединение должно выдерживать нагрузку на растяжение. При такой конструкции припой не проходит на запрессованный стержень из-за отсутствия зазора между деталями. Прочность пайки оказывается недостаточной, так как деталь припаивается только фаской.
Правильная конструкция соединения в таком случае, в то же время более простая и дешевая, показана на фиг. 30, б.
При такой конструкции пайка получается качественной и прочной.
По условиям технологии в обоих вариантах после пайки детали проходят механическую обработку.
15. При соединении деталей пайкой нужно следить за тем, чтобы они имели равномерный зазор по всему периметру соединения (фиг. 31,6). При плохой и неряшливой подгонке (фиг. 31, а) после пайки получаются утяжки или выпучины вследствие неравномерного распределения слоя припоя. Выпучины получаются в сторону более тонкой стенки.
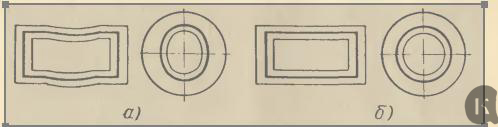
Фиг. 31. Зазор при пайке.
а—неправильная подгонка деталей друг к другу; б—правильная подгонка деталей друг к другу
16. На фиг. 32, а показана втулка 1 с указанными размерами, которая должна быть вставлена в основание 2 и спаяна, как указано 3. Это конструкция неудачна для пайки и спаять ее указанным способом не представляется возможным, так как размеры втулки и основания при соединении не обеспечивают зазоров под пайку. Имеющаяся на втулке фаска отрицательно сказывается на пайке. Плохо также то, что припой должен пройти три ступени.
На фиг. 32, б показано, как должно быть правильно изготовлено посадочное отверстие под втулку с зазорами для пайки. Если позволяет основание конструкции 2, желательно расточить отверстие до диаметра 24 мм. Нужно также предусмотреть (см. фиг. 32, вид по стр. А) на торце втулки канавки. Во время пайки, когда мы прижмем втулку к основанию грузом, припой пойдет по> этим канавкам и выйдет на технологический припуск 4 на торце втулки.
17. В различных конструкциях, в местах, в которых детали будут припаиваться друг к другу, применять резьбовые соединения не рекомендуется (фиг. 33), так как это влечет за собой излишний расход припоя и удорожание самого изделия, не улучшая по существу соединения. Припой при пайке в таких случаях пойдет не только в местах соединения этих деталей, но и по нарезанной резьбе.
18. Расположение мест пайки различных деталей к цилиндру должно быть таким, чтобы все пайки или большинство из них можно было выполнить при вертикальном положении цилиндра. Перед началом пайки детали на поверхности обточенного цилиндра устанавливаются на шпильки или штифты (фиг. 34). В деталях должны быть заранее предусмотрены технологические отверстия для крепления их на цилиндре. Отверстие а цилиндра нужно изготовлять с припуском 2 мм на сторону при диаметре цилиндра до- 60 мм и 3—4 мм
на сторону при диаметре от 60 до 150 мм Окончательная обработка отверстия производится после пайки, так как во время пайки внутренняя поверхность цилиндра, особенно у тонкостенных деталей (с толщиной стенки до- 4 мм), может покоробиться.
19. При изготовлении паяного узла (фиг. 35), который состоит из двух щек 1 и обечайки 2, производится следующая технологическая подготовка.
Вид по стрелке
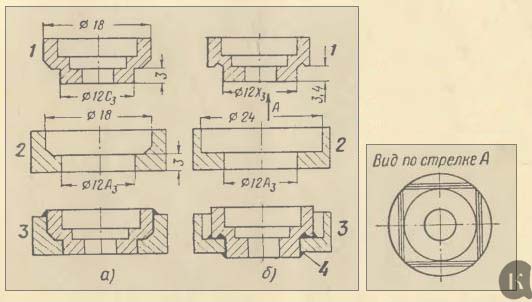
Фиг. 32. Паяный узел.
а—неправильная конструкция; б—правильная конструкция.
На деталях 1 с внутренней стороны по контуру детали 2 наносятся установочные риски глубиной 0,2 и шириной 0,2 мм. Необходимо предусмотреть и технологический припуск на деталь 1 в 0,5—
2 мм для правильного расположения припоя во время пайки. Перед пайкой детали 1 и 2 соединяются струбцинами или проволокой, затем они припаиваются в нескольких точках. После этого струбцины и проволока снимаются и производится окончательная пайка. После пайки производится обработка технологического припуска заподлицо 1ПО контуру детали 2.
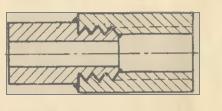
Фиг. 33. Соединение труб с резьбой.
20. Разберем пример, когда требуется спаять узел (фиг. 36), который состоит из втулки 2, шпонки 3 и стенки трубы 1.
Конструкция узла предусматривает припайку шпонки 3 твердым припоем, однако опыт показывает, что производить пайку шпонки не имеет смысла, так как обычно шпонки плотно вставляются в свои гнезда. При соединении узлов такого типа необходимо предусматривать обработку стенки торца детали 1 после припайки к ней детали 2, так как торцевое соединение после пайки получается недостаточно правильным из-за коробления детали 1.
21. Рассмотрим случай (фиг. 37), когда требуется припаять к трубе 2 две детали — 1 и 3, вставленные в отверстия с необходимыми зазорами для пайки. Припаять деталь 1 к трубе 2 можно, как
показано на фигуре, с выходом припоя внутрь. Это обеспечивает прочность паяного соединения. При переходе к пайке детали 3 с другой стороны трубы пайка может получиться некачественной, так как припой не пойдет внутрь и останется только на фаске, как показано на фигуре. Поэтому рекомендуется при конструировании
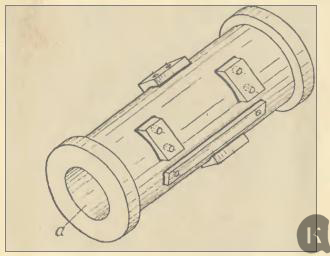
Фиг. 34. Технологическое крепление деталей ка цилиндре для цайки.
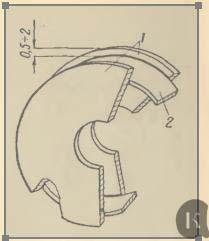
Фиг. 35. Пайка с технологическими припусками на щеках.
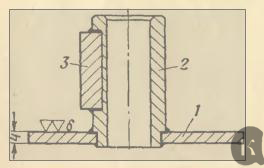
Фиг. 36. Паяный узел из трех деталей.
а—неправильная конструкция; б—правильная конструкция.
14. На фиг. 30, а показана неправильная конструкция двух спаиваемых деталей. В стержень / запрессовывается деталь 2, которая затем должна быть припаяна. Под пайку оставлена на детали фаска
0,5X45°.
По условиям работы соединение должно выдерживать нагрузку на растяжение. При такой конструкции припой не проходит на запрессованный стержень из-за отсутствия зазора между деталями. Прочность пайки оказывается недостаточной, так как деталь припаивается только фаской.
Правильная конструкция соединения в таком случае, в то же время более простая и дешевая, показана на фиг. 30, б.
При такой конструкции пайка получается качественной и прочной.
По условиям технологии в обоих вариантах после пайки детали проходят механическую обработку.
15. При соединении деталей пайкой нужно следить за тем, чтобы они имели равномерный зазор по всему периметру соединения (фиг. 31,6). При плохой и неряшливой подгонке (фиг. 31, а) после пайки получаются утяжки или выпучины вследствие неравномерного распределения слоя припоя. Выпучины получаются в сторону более тонкой стенки.
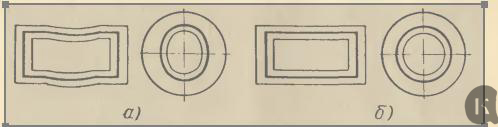
Фиг. 31. Зазор при пайке.
а—неправильная подгонка деталей друг к другу; б—правильная подгонка деталей друг к другу
16. На фиг. 32, а показана втулка 1 с указанными размерами, которая должна быть вставлена в основание 2 и спаяна, как указано 3. Это конструкция неудачна для пайки и спаять ее указанным способом не представляется возможным, так как размеры втулки и основания при соединении не обеспечивают зазоров под пайку. Имеющаяся на втулке фаска отрицательно сказывается на пайке. Плохо также то, что припой должен пройти три ступени.
На фиг. 32, б показано, как должно быть правильно изготовлено посадочное отверстие под втулку с зазорами для пайки. Если позволяет основание конструкции 2, желательно расточить отверстие до диаметра 24 мм. Нужно также предусмотреть (см. фиг. 32, вид по стр. А) на торце втулки канавки. Во время пайки, когда мы прижмем втулку к основанию грузом, припой пойдет по> этим канавкам и выйдет на технологический припуск 4 на торце втулки.
17. В различных конструкциях, в местах, в которых детали будут припаиваться друг к другу, применять резьбовые соединения не рекомендуется (фиг. 33), так как это влечет за собой излишний расход припоя и удорожание самого изделия, не улучшая по существу соединения. Припой при пайке в таких случаях пойдет не только в местах соединения этих деталей, но и по нарезанной резьбе.
18. Расположение мест пайки различных деталей к цилиндру должно быть таким, чтобы все пайки или большинство из них можно было выполнить при вертикальном положении цилиндра. Перед началом пайки детали на поверхности обточенного цилиндра устанавливаются на шпильки или штифты (фиг. 34). В деталях должны быть заранее предусмотрены технологические отверстия для крепления их на цилиндре. Отверстие а цилиндра нужно изготовлять с припуском 2 мм на сторону при диаметре цилиндра до- 60 мм и 3—4 мм
на сторону при диаметре от 60 до 150 мм Окончательная обработка отверстия производится после пайки, так как во время пайки внутренняя поверхность цилиндра, особенно у тонкостенных деталей (с толщиной стенки до- 4 мм), может покоробиться.
19. При изготовлении паяного узла (фиг. 35), который состоит из двух щек 1 и обечайки 2, производится следующая технологическая подготовка.
Вид по стрелке
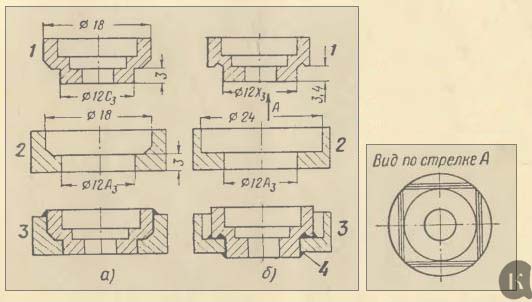
Фиг. 32. Паяный узел.
а—неправильная конструкция; б—правильная конструкция.
На деталях 1 с внутренней стороны по контуру детали 2 наносятся установочные риски глубиной 0,2 и шириной 0,2 мм. Необходимо предусмотреть и технологический припуск на деталь 1 в 0,5—
2 мм для правильного расположения припоя во время пайки. Перед пайкой детали 1 и 2 соединяются струбцинами или проволокой, затем они припаиваются в нескольких точках. После этого струбцины и проволока снимаются и производится окончательная пайка. После пайки производится обработка технологического припуска заподлицо 1ПО контуру детали 2.
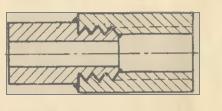
Фиг. 33. Соединение труб с резьбой.
20. Разберем пример, когда требуется спаять узел (фиг. 36), который состоит из втулки 2, шпонки 3 и стенки трубы 1.
Конструкция узла предусматривает припайку шпонки 3 твердым припоем, однако опыт показывает, что производить пайку шпонки не имеет смысла, так как обычно шпонки плотно вставляются в свои гнезда. При соединении узлов такого типа необходимо предусматривать обработку стенки торца детали 1 после припайки к ней детали 2, так как торцевое соединение после пайки получается недостаточно правильным из-за коробления детали 1.
21. Рассмотрим случай (фиг. 37), когда требуется припаять к трубе 2 две детали — 1 и 3, вставленные в отверстия с необходимыми зазорами для пайки. Припаять деталь 1 к трубе 2 можно, как
показано на фигуре, с выходом припоя внутрь. Это обеспечивает прочность паяного соединения. При переходе к пайке детали 3 с другой стороны трубы пайка может получиться некачественной, так как припой не пойдет внутрь и останется только на фаске, как показано на фигуре. Поэтому рекомендуется при конструировании
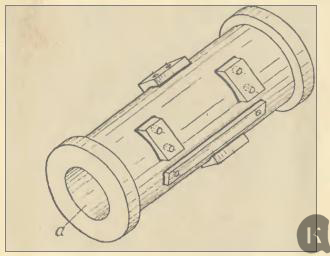
Фиг. 34. Технологическое крепление деталей ка цилиндре для цайки.
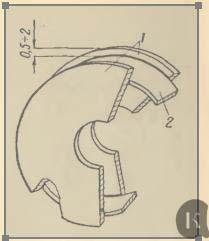
Фиг. 35. Пайка с технологическими припусками на щеках.
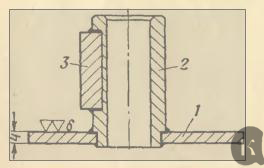
Фиг. 36. Паяный узел из трех деталей.
подобных деталей предусматривать отверстия (Л или В) для циркуляции воздуха. Эти отверстия могут быть впоследствии использованы как резьбовые или штифтовые или же могут после пайки заделываться. Обычно после пайки конструкций, подобных разобранной
нами, производится окончательная механическая обработка.
22. Способ наложения флюса на соединяемые пайкой детали в местах их соединения, т. е. в местах образования шва, имеет большое значение для экономии припоя.
Есть два вида наложения флюса:
а) Флюс, замешенный на воде . или спирте, наносится в местах будущего шва до пайки,
б) Флюс наносится во время самой пайки или в промежутках между ней; в этом случае применяют буру в виде порошка, щепотки которого бросают на горячие детали.
На спаиваемые детали 1 и 2 (фиг. 38) Наложен флюс 3, замешенный на воде. Во время нагрева флюс вспенивается (от присутствия влаги) и омывает, т. е. очищает язычками поверхность, большую, чем это нужно для прохождения припоя. Припой же попадает впоследствии на всю очищенную флюсом поверхность. Таким образом, получится излишний расход припоя. Иногда это приводит и
к излишней дальнейшей обработке. Поэтому лучше всего наносить заранее флюс, замешенный на спирте.
23. Рассмотрим случай, когда требуется спаять втулку 2 (фиг. 39) с наружной стенкой трубы 1. Деталь заранее покрывается флюсом в местах прохождения припоя, и втулка вставляется на свое место. Обычно паяльщик кладет на деталь 2 легкий груз 3, вес которого подбирается по условиям и сложности паяния. Груз служит для того* чтобы во время пайки втулка не приподнималась при прохождении
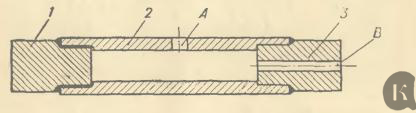
Фиг. 37. Пайка трубы с заглушками с технологическими отверстиями.
припоя и при вспенивании влаги (если флюс разведен на воде), а также для фиксирования положения втулки на трубе. Груз является также компенсатором температуры при пайке разностенных деталей и предохраняет тонкие детали от прогорания. Обычно этот груз изготовляется из стали; вес его и размеры подбираются опытным путем в процессе паяния.
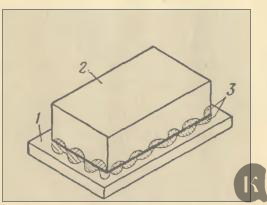
Фиг. 38. Положение флюса во время пайки.
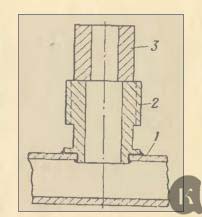
Фиг. 39. Пайка с компенсатором.
24. При пайке тонкостенных деталей с толщиной стенки до 2 мм (детали 1 и 2 на фиг. 40) при нагреве из-за неопытности паяльщика может произойти прожог тонкой стенки. От этого предохраняют фиксаторы-компенсаторы. Они же служат для фиксации втулки по отверстию трубы (правая сторона) и как оправка, предохраняющая от коробления стенки и фиксирующая диаметр, особенно, если отверстие изготовлено по 3-му классу точности. Компенсаторы могут быть различны по своей форме. Грузы-компенсаторы рекомендуется изготовлять для предохранения прожога деталей со стенками до двух мм. Это особенно важно, если детали с тонкой стенкой имеют толстую стенку основания.
25. В случае, показанном на фиг. 41, требуется припаять резьбовую втулку 2 к наружной стенке трубы 1. Втулка находится в своем -отверстии очень низко буртиком, так как резьба втулки расположена почти на одной поверхности с накладкой трубы (расстояние всего 2 мм).
Во время пайки этих деталей припой заходит на резьбу, что вы-
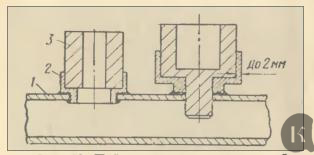
Фиг. 40. Пайка тонкостенных деталей с фиксатором-компенсатором.
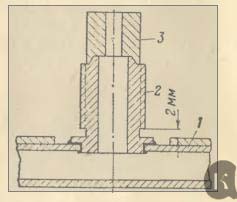
Фиг. 41. Пайка резьбовой втулки к наружной стенке трубы.
зывает впоследствии большие трудности — приходится калибровать резьбу после пайки.
При конструировании подобных узлов необходимо предусматривать, чтобы бортик втулки 2 находился бы на уровне верхней плоскости детали /, а не в углублении, как показано на фигуре.
В случае же, если конструкция выполнена так, как показано на фигуре, поступают следующим образом. Места образования шва зафлюсовывают как обычно, а резьбу втулки покрывают пастой из мела или графита или их смеси, замешенных на воде. Можно также изолировать резьбу смоченным водой асбестом, но этим способом паяльщики пользуются неохотно, так как во время нагревания некоторые нити асбеста загораются и горят очень ярким пламенем. Показанная на фигуре деталь 3 является компенсатором.
26. Близкое расположение мест пайки ведет к затруднению процесса пайки. Пайка узла, показанного на фиг. 42, производится следующим образом. Пластины 3 вставляются с двух сторон в пазы, которые имеются на трубе 1, и покрываются флюсом внутри трубы. Флюс наносится ровной полоской в местах образования шва. Чтобы пластины 3 не выпадали из своих мест, производят подогревание флюса до его стеклообразного состояния. Затем соединяют детали 2 и 1, покрывают их флюсом и устанавливают деталь 1 вертикально на детали 2. После этого- производят
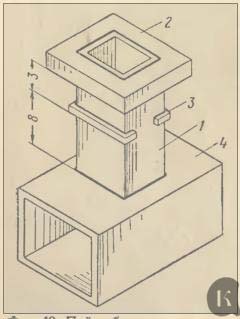
Фиг. 42. Пайка близко расположенных швов.
пайку детали 2; так как расстояния между швами спайки детали/с деталью 2 и детали 1 с деталью 3 всего 3 мм и температура в обоих швах одинакова, то припой одновременно забегает Б оба шва. Затем деталь 1 устанавливают на детали 4 и производят последнюю пайку узла.
Пайка близко расположенных швов (на расстоянии 3 мм и менее) одним припоем представляет собой очень большие трудности,
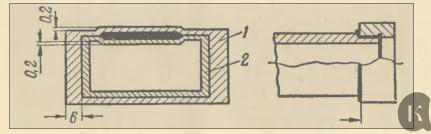
Фиг 43. Утяжки и выпучины от пайки.
так как при каждой отдельной пайке может быть распаян предыдущий шов. В таких случаях лучше всего производить ступенчатую пайку припоями с различными температурами плавления.
27. При соединении пайкой деталей 1 и 2 (фиг. 43), имеющих толщину стенок до 2 мм, может получиться выпучина до 0,2 мм, как
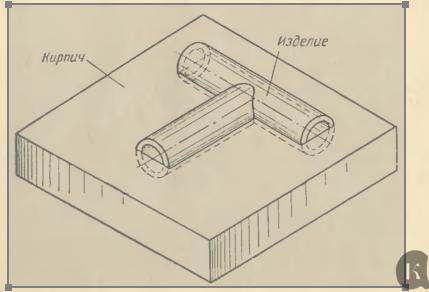
Фиг. 44. Простое приспособление для пайки.
указано на фигуре. Это происходит из-за неравномерности зазора, коробления, неравномерного прогрева во время пайки, неряшливой подгонки деталей друг к другу перед пайкой. Чтобы избежать выпу-чин, необходимо вставлять внутрь деталей оправки или скобки, чтобы внутренний контур остался правильным. Оправки должны быть пустотелыми и из того же материала, что и спаиваемые детали, чтобы избежать излишнего нагрева.
28. При пайке мелких деталей (фиг. 44) припоями, указанными в таблице, например, латунных трубок с толщиной стенки 0,5 мм
при наружном диаметре 6 мм, пользуются как приспособлением для пайки кирпичом. Для этого в огнеупорном кирпиче выдалбливают или высверливают наружный контур, который будет иметь деталь в собранном виде. Пайка указанных трубок производится горелками мелких номеров. Нужно предварительно нагреть детали в местах соединения, затем ввести в места пайки значительную порцию порошкообразного флюса (буры), который при расплавлении до стеклообразного состояния стягивает трубки, что обеспечивает плотное прилегание их друг к другу, а затем быстро вводить при нагреве небольшую порцию припоя. Такое приспособление просто и дешево и рекомендуется для мелкосерийного производства.
29. Пайка колец из ленты (фиг. 45) не представляет собой большой трудности, но требует внимательного и аккуратного исполнения.,
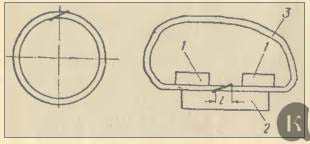
Фиг. 45. Пайка сепараторного кольца.
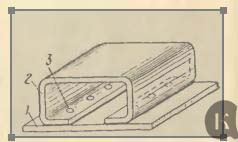
Фиг. 46. Соединение заклепками перед пайкой.
Длина развертки заготовки кольца отрезается в размер. При пайке паяльщик сгибает отрезок ленты, как показано на фигуре с правой стороны, устанавливает его на кирпич 2 и прижимает заготовку кольца 3 двумя грузами 1. На концах заготовки в местах соединения сделаны заранее скосы с каждой стороны на длину 1—7 мм Место шва покрываетс51 флюсом и производится пайка, а затем зачистка паяного шва, деталь 3 рихтуется на цилиндрической оправ ке и, если необходимо, производится механическая обработка. Таким же образом производится обработка специальных сепараторных колец, только отверстия по координатам для шариков обрабатываются и растачиваются в развертке.
30. При фиксации перед пайкой детали 2 на детали 1 (фиг. 46) можно избежать изготовления приспособлений для пайки. Лучше всего фиксацию производить заклепками из этого же материала. Клепку производить не окончательно, а с люфтом, чтобы припой смог проходить по всей плоскости. С введением заклепочных соединений появилась возможность перевести указанную деталь на пайку мягкими припоями вместо серебряного припоя.
31. Пайка контактов на многих производствах довольно трудоемка, так как обычно паять их приходится значительное количество, а мелкие размеры контактов и высокие требования к качеству пайки заставляют паяльщика быть особенно внимательным.
Контакт (фиг. 47) состоит из чашки 1, которая изготовляется из стали, и собственно контакта 2— вольфрамового или платинового. Для получения собранного контакта 3 нужно деталь 2 впаять в чаш-
ку 1. Для этого в чашечке 1 зафлюсовывают место припайки контакта и прогревают флюс, пока он не затвердеет. Когда мы наносим флюс внутри чашечки, надо следить за тем, чтобы он на 1 мм не доходил до отверстия е, иначе припой при нагреве будет скатываться в отверстие. Затем кладут в чашечку отрубленное кусачками маленькое зерно припоя и плавят его для того, чтобы припой расположился по краям чашки. После этого вставляют контакт 2 в чашку/и производят окончательный нагрев. Иногда при этом слегка нажимают на контакт, чтобы выдавить излишний припой.
Для того чтобы ускорить обработку контактов, делают простое приспособление 4 из латуни или стали на двадцать и больше гнезд
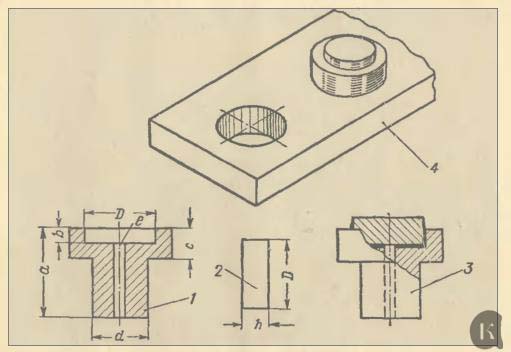
Фиг. 47. Пайка контактов.
с определенным шагом между отверстиями для контактов. После того как поставлены все контакты, работа производится по операциям, что намного увеличивает производительность труда паяльщика.
При пайке контактов иногда делают и так: листовой припой типа фольги разрезают на мелкие кусочки («глазки», как их называют паяльщики), место пайки покрывают флюсом и вкладывают глазок в гнездо контакта, а на припой сверху накладывают сам контакт; затем производят нагрев до расплавления припоя, и контакт Под действием собственной тяжести входит на свое место. Надо проследить за тем, чтобы контакт по всей поверхности вошел в гнездо До отказа. По окружности контакта должна выступить ровная полоска припоя. Пайка контактов с применением припоя в виде фольги наиболее эффективна.
32. Простое приспособление (фиг. 48) для пайки трубы с одним Коленом состоит из следующих деталей: корпуса 3, направляющих
стержней 4, 5 и 6 для фиксации трубы и колена. При установке в приспособление труба 1 одним концом надевается на неподвижный стержень 5, а другой ее конец фиксируется подвижным стержнем 4. Колено фиксируется стержнем 6 и закрепляется в приспособлении винтами. Нужно учитывать во время пайки расширение
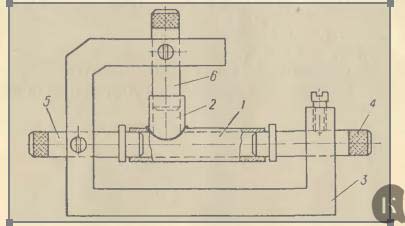
Фиг. 48. Пайка трубы под углом 90° на приспособлении.
латунных трубок от нагрева и направляющие стержни вплотную к трубам не прижимать. При пайке без приспособления отверстия труб получают овальную форму. Например, отверстие диаметром 13 мм после пайки имеет овальность 0,2 мм. При пайке с приспособлением овальности отверстий не получается. Рассмотренное
приспособление удобно при мелкосерийном производстве и дешево в изготовлении.
33. Требуется припаять (фиг. 49) к наружным стенкам трубы 2 втулки 1 и 3 и выдержать при этом после пайки
соосность отверстий между
втулками с точностью до
0,035 мм. Для пайки втулок изготовляется оправка 4, которая фиксируется на конус втулки/и цилиндрическую часть втулки 3 (допуск по 3-му классу
точности). Иногда (при больших диаметрах втулок) на торцах
втулок, соприкасающихся со стенками трубы 2, пропиливают надфилем канавки шириной 0,3 мм и глубиной 0,2 мм в форме треугольника. Это делается для того, чтобы был обеспечен проход припоя на торцы втулок. Места пайки втулок покрывают тонким слоем сильно измельченного флюса. Если слой Флюса больше необходимого, то во время пайки, когда мы прижмем втулку грузом, флюс может не выйти из-под торца втулок. Затем оправка 4 вставляется в коническое отверстие втулки 1 и закрепляется гайкой с шайбой. Полную затяжку втулки на конус производить не рекомендуется, а следует оставлять едва заметный люфт (это делается
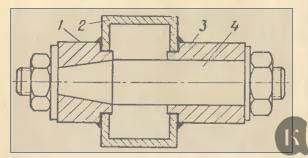
Фиг. 49. Соблюдение соосности отверстия во время пайки.
в связи с расширением металла во время нагрева). Затем с цилиндрической части оправки с заметным люфтом закрепляется гайка с шайбой. Порядок пайки следующий: деталь 2 помещают между двух кирпичей втулкой 3 вверх. Производится пайка втулки 3 к стенке трубы 2. Затем таким же образом производится пайка втулки 1. Как только процесс пайки закончен, необходимо без промедления отвернуть гайку со стороны втулки 1 и легким ударом, вынуть оправку. При пайке мы выдерживаем соосность между отверстиями втулок с точностью до 0,1 мм, так как после освобождения оправки 4 спаянный узел еще горячий и, остывая, коробится. Оставлять оправку до полного остывания нельзя, так как при остывании ее может зажать (латунные части остывают быстрее, чем стальная оправка). Чтобы выдержать установленную соосность с
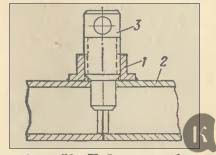
Фиг. 50. Пайка резьбовой втулки на оправке.
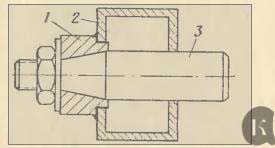
Фиг. 51. Пайка втулки на оправке с фиксацией на резьбу в другой детали.
точностью 0,0,35 мм, предусматривают механическую обработку шда специальную развертку. Рассмотренный случай требует большой квалификации паяльщика и соответствующей подготовки к выполняемой работе.
34. В узле, показанном на фиг. 50, требуется выдержать соосность при пайке между резьбовой частью втулки и отверстием трубы с точностью до 0,1 мм. Для изготовления узла с заданной точностью необходимо изготовить стальную оправку 3 с фиксацией на отверстие в трубе 2 и резьбовую часть втулки 1.
Необходимо предусмотреть, чтобы при механической обработке-соприкасающийся торец втулки 1 был изготовлен на базе резьбового отверстия. Перед пайкой втулка 1 надевается на оправку 3 и фиксируется в отверстие трубы 2. Конец резьбовой оправки и ее цилиндрическая часть иногда покрываются мелом, чтобы избежать возможного припаивания к втулке 1. Покрытия флюсом места пайки заранее производить не рекомендуется. В начале пайки прихватывают припоем с одной стороны втулку 1 к трубе 2 и еще горячей вывертывают оправку 3. После того, как мы освободились от оправки 3, пайку производят обычным порядком, предварительно положив на втулку 1 легкий груз (чтобы не допустить сдвига ее с места).
После пайки необходимо произвести калибровку резьбы во* втулке 1.
35. Панка (фиг. 51) втулки 1 с фиксацией на резьбовое отверстие противоположной стенки трубы не представляет большой труд-
пости. Аналогичный случай показан на фиг. 49 и 50. Разница лишь в том, что в рассматриваемом примере оправку 3 необходимо фиксировать на резьбовое отверстие. Соосность между коническим отверстием втулки I и резьбовой частью противоположной стенки трубы 2 можно выдержать с точностью 0,2 мм.
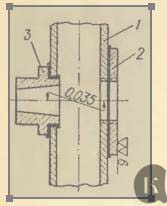
Фиг. 52. Технологические припуски для обработки после пайки.
36. В примере, показанном на фиг. 52, требуется припаять к наружным стенкам трубы 1 окончательно обработанную втулку 3 и накладку 2, которая должна обрабатываться по торцу с расточкой и нарезкой резьбы после пайки. В первую очередь мы производим припайку втулки 3 к трубе 1 (так же, как описано в 'примере, показанном на фиг. 36). Затем производим припайку накладки 2 к трубе 1. В накладке 2 и трубе 1 предусмотрено технологическое отверстие для фиксации их совместно на оправке при пайке (после пайки это технологическое отверстие растачивается до размеров заданного резьбового отверстия). После пайки необходимо зачистить торец втулки 3 с внутренней стороны трубы заподлицо со стенкой. После этого растачиваем отверстие и нарезаем резьбу с одновременной подрезкой торца под УУ 6 до нужного размера. Чтобы выдержать соосность с точностью 0,035 мм, расточку и нарезание резьбы производят на токарном станке с фиксацией на конической оправке с гайкой.
В случаях, подобных разобранному, механическую обработку резьбы и торца нужно производить после пайки. Выдержать соос-
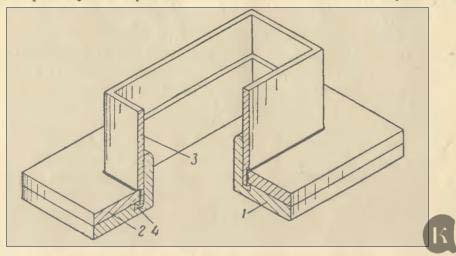
Фиг 53. Пайка трубы с фланцем на оправке.
ность 0,035 мм при пайке тонких стенок очень трудно и в таких случаях необходимо предусматривать технологические припуски, так как тонкие стенки конструкции сами по себе не обеспечивают этих допусков.
37. Часто требуется припаивать (фиг. 53) к трубе 3 фланец 2 так, чтобы они были взаимно перпендикулярны. Для этого изготовляют
простую пустотелую оправку 1. Труба 3 фиксируется на это приспособление своим внутренним контуром. На оправке I предусмотрены фаски 4 и канавки, которые перед пайкой покрывают мелом или графитом (или их смесью), чтобы во время пайки оправка не припаялась к приспособлению. Кроме того, оправка предохраняет внутренний контур трубы от коробления.
Если спаиваются труба и фланец больших размеров, то оправку применять не рекомендуется, так как в этом случае в месте спая получается раковичностъ. Тог-
да, чтобы избежать коробления, вместо оправки вставляется специальная латунная скоба.
38. Необходимо припаять (фиг. 54) трубу I с длинным (больше 300 мм) концом от радиуса изгиба к фланцу 2.
Нужно правильно установить трубу 1 и фланец 2 — обеспечить угол 9СР между осью трубы и осью фланца. Для этого применяется подставка 3.
На торец фланца должен давить груз 6, который прижимает фланец к подкладке и не
позволяет ему подыматься и коробиться во время пайки. Груз 6 не должен мешать паяльщику во время работы. Пластина 4 покоится на кирпичном основании 5. После пайки узел должен остывать вместе с подставкой и грузом, чтобы не было коробления. Если не
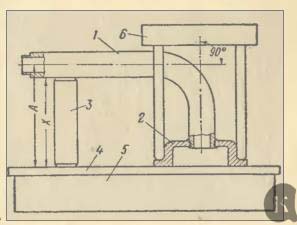
Фиг. 54. Пайка фланца с длинной трубой.
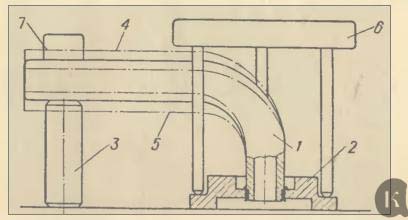
Фиг. 55. Исправление брака после пайки.
пользоваться описанными приспособлениями, труба 1 может принять неправильное положение, как показано пунктирными линиями 4 и 5 на фиг. 55. Обыкновенно такие ненормальности пайки не всегда можно исправить обычной слесарной рихтовкой. Выправить узел можно следующим образом. Нужно установить размерную оправку 3 и наложить груз 6 на фланец 2, а также наложить груз 7, который через трубу 1 опирается на подставку 3. Затем нагреваем
место пайки. За счет зазоров под пайку труба 1 займет правильное положение. После этого пропаиваем узел вторично.
39. В случае, изображенном на фиг. 56, требуется спаять детали 1,2,3 я 4. Для пайки необходимо изготовить простое приспособление в виде стального четырехмиллиметрового угольника 5. На угольнике расставлены шпильки 8 для фиксации детали во время пайки. Шпильки рассчитаны так, чтобы при расширении металла от нагревания они не упирались во фланцы и не оставляли на них вмятин.
Если труба 2 выходит за торец фланцев 1 и 3, то нужно сделать окошки-прорези в угольнике 5. Последовательность пайки следующая: производят сборку деталей 1, 2, 4 и 3, покрывают флюсом места соединения детали 2 с деталями 1 и 3; планка 4 устанавливается в вертикальное положение; устанавливается подставка 9 под трубу, предварительно рассчитанная по заданным размерам; затем производится припайка детали 3 к детали 2; после этого снимают оправку 9, перевертывают угольник 5 в нижнее положение для пайки детали 1. После спайки детали 1 с деталью 2 перевертывают угольник в первоначальное положение, деталь 4 устанавливается на подставки 7, которые заранее определены размерами чертежа для установки детали 4. На детали 4 перед пайкой устанавливается груз 6 (что предохраняет от коробления).
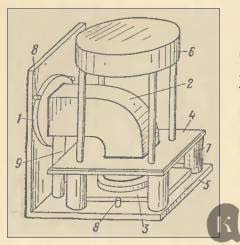
Фиг. 56. Пайка узла на приспособлении.
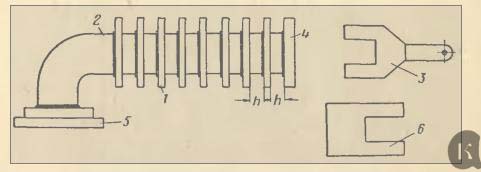
Фиг. 57. Пайка к трубе фланцев и пластин.
40. Необходимо припаять (фиг. 57) к трубе 2 фланцы 4 и 5 и также пластины 1 (8 штук) с размером между ними к. Пайка фланцев 4 и 5 к трубе 2 не отличается от описанной выше в подобных примерах. После припайки фланцев 4 и 5 все пластины для удобства пайки передвигаем к фланцу 5. В этом положении они удерживаются специально изготовленным для этой цели крючком из жести. Труба 2 устанавливается в вертикальное положение. Чтобы избежать разметки места каждой пластины на трубе 2 и не затруднять
паяльщика установкой их на расстояние к друг от друга, изготовляется простое приспособление 3 в виде вилки. Перед пайкой вилка 3 кладется на торец фланца 4, сверху опускается пластина для пайки, на шайбу накладывается дополнительно компенсатор 6 из стали или чугуна — так, чтобы остался свободный проход для удобства пайки. После этого производится пайка пластины. Затем компенсатор и вилка переставляются для пайки следующей пластины и т. д. Плоскость вилки 3, которая соприкасается с шайбами, должна быть покрыта мелом или графитом (или их смесью). Эти простые оправки намного увеличивают производительность труда паяльщика.
41. Требуется спаять (ф.иг. 58) детали 2, 3 и 5. В1 первую очередь производят пайку деталей 2 и 3 на приспособлении, как указано на фиг. 53. Затем производится подготовка к пайке уже спаянного узла с деталью 5 — устанавливается оправка 1 на технологическое отверстие в цилиндре 5.
Чтобы деталь 2 не припаялась к оправке, на оправке 1 сделаны в местах пайки фаски 4 (3X45°), а плоскости оправки 1, соприкасающиеся с деталью 5, и фаски на оправке покрываются мелом, графитом или их смесью. Нагревают в первую очередь массивные места детали 5. Отверстие диаметром О в цилиндре расточено предварительно, а после пайки оно' обрабатывается по 3-му классу точности. При пайке нескольких патрубков угол между их осями можно выдержать с точностью -Ц5'.
Если припаивать к цилиндру два или несколько патрубков, то даже при сравнительно толстых стенках цилиндра все же получается коробление. Поэтому при точных работах необходимо отверстие и наружный диаметр цилиндра изготовлять с припуском под окончательную обработку после пайки.
42. Требуется припаять (фиг. 59) трубы /, 2 и 3 к пластине 4. Нужно выбрать базы для фиксации труб во время пайки. В трубах /, 2 и 3 и пластине 4 после пайки должны быть расточены отверстия по 3-му классу точности, которые по координатам связаны между собой по 4-му и 5-му классам точности. Чтобы правильно собрать и спаять трубы и пластину, на месте будущих отверстий сделаны четыре технологических отверстия диаметром 4А4 в пластине и в одной стенке в трубах. Предусмотрены также технологические припуски по 2 мм на каждую сторону в пластине 4, которые после окончательной пайки обрабатываются механическим путем заподлицо с трубами 1 и 3. Эти технологические припуски нужны для того, чтобы припой во время пайки не скатывался.
Для фиксации во время пайки всех деталей было изготовлено простое приспособление 5, которое копировало по наружному кон-
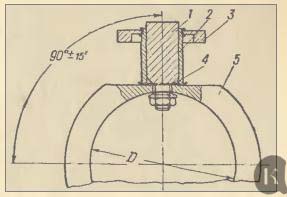
Фиг 58. Пайка трубы с фланцем к цилиндру на приспособлении.
туру форму пластины 4. На этом приспособлении были изготовлены четыре фиксатора диаметром 4С4. Перед пайкой на этом приспособлении необходимо подогнать зазоры для пайки между местами соединения в трубах с таким расчетом, чтобы учесть линейное расширение металла при нагревании. Необходимо также просверлить несколько технологических отверстий в приспособлении 5 и в пластине 4 в местах, которые соответствуют соединениям труб между собой, для того чтобы во время пайки не образовывалось воздушных мешков. Если этого не сделать, то припой на всю глубину не прой-
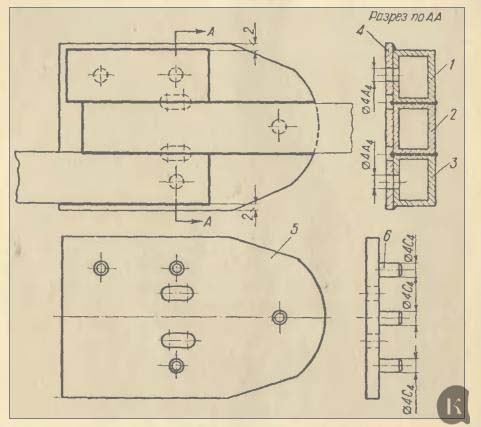
Фиг. 59. Сложная пайка труб к пластине.
дет, а стенки труб должны быть спаяны на всей длине и глубине соединения. Вначале необходимо припаять (прихватить) в шести точках, для того чтобы зафиксировать окончательное положение труб на пластине. После этого пайка производится в обычном порядке. Во время пайки необходимо наблюдать за тем, чтобы нагрев всех деталей был равномерным, так как в противном случае может получиться кривизна (выпуклость и вогнутость до 0,2 мм на длине 100 мм). После пайки в рассмотренном примере нужно произвести травление, зачистку мест пайки, рихтовку на разжимных стальных клиновых оправках или оправках по внутреннему контуру из фибры, текстолита или дельта-древесины.
43. Необходимо впаять (фиг. 60) в пазы трубы 1 пластины 2. Пластины 2 необходимо подобрать так, чтобы между пластиной и стенками трубы (с обеих сторон) оставался зазор. Пластины долж-36
ны выходить за контур трубы не менее чем по 1 мм на сторону. Это необходимо для того, чтобы с каждой стороны пластины можно было положить по кусочку припоя и припой не перекатывался бы на одну сторону. Иначе припой при расплавлении сосредоточится в одном месте и заполнит зазоры неравномерно.
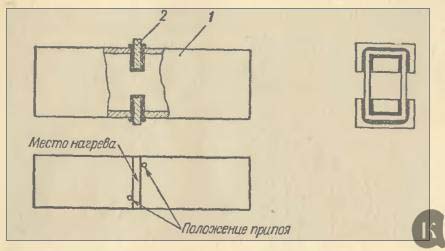
Фиг. 60. Пайка тонких пластин к трубе.
При подготовке к пайке необходимо: вставив пластинку в пазы, покрыть их флюсом с наружной части трубы и, держа деталь пассатижами в руках, подогреть флюс до его затвердевания. Как только флюс затвердеет, он будет удерживать пластины от выпадания и смещения из своих гнезд. После остывания детали необходимо произвести зафлюсовку (уже внутри трубы) стенок трубы и пластины. Флюс внутри трубы на пластине 2 в местах соединения с трубой 1 накладывать очень осторожно ровной полоской шириной не более 1 мм, так как по условиям изготовления детали разрешается выход припоя внутрь пластин фаской шириной не более 1 мм.
Нагрев производится в средней части пластины 2, для того чтобы припой расплавлялся одновременно и заполнял зазоры с каждой стороны равномерно, не прижимая пластину к какой-либо одной стороне. После пайки деталь поступает на дальнейшую обработку — для запиловки технологического припуска заподлицо с наружным контуром.
44. Необходимо припаять (фиг. 61) к наружной стенке трубы 1 втулку 2 и крышку 3. Для удобства пайки лучше всего начинать пайку с детали 2. Перед пайкой места спая на втулке и в отверстии трубы покрываются флюсом.
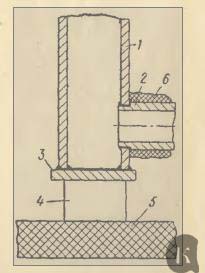
var container = document.getElementById('nativeroll_video_cont'); if (container) { var parent = container.parentElement; if (parent) { const wrapper = document.createElement('div'); wrapper.classList.add('js-teasers-wrapper'); parent.insertBefore(wrapper, container.nextSibling); } }
нами, производится окончательная механическая обработка.
22. Способ наложения флюса на соединяемые пайкой детали в местах их соединения, т. е. в местах образования шва, имеет большое значение для экономии припоя.
Есть два вида наложения флюса:
а) Флюс, замешенный на воде . или спирте, наносится в местах будущего шва до пайки,
б) Флюс наносится во время самой пайки или в промежутках между ней; в этом случае применяют буру в виде порошка, щепотки которого бросают на горячие детали.
На спаиваемые детали 1 и 2 (фиг. 38) Наложен флюс 3, замешенный на воде. Во время нагрева флюс вспенивается (от присутствия влаги) и омывает, т. е. очищает язычками поверхность, большую, чем это нужно для прохождения припоя. Припой же попадает впоследствии на всю очищенную флюсом поверхность. Таким образом, получится излишний расход припоя. Иногда это приводит и
к излишней дальнейшей обработке. Поэтому лучше всего наносить заранее флюс, замешенный на спирте.
23. Рассмотрим случай, когда требуется спаять втулку 2 (фиг. 39) с наружной стенкой трубы 1. Деталь заранее покрывается флюсом в местах прохождения припоя, и втулка вставляется на свое место. Обычно паяльщик кладет на деталь 2 легкий груз 3, вес которого подбирается по условиям и сложности паяния. Груз служит для того* чтобы во время пайки втулка не приподнималась при прохождении
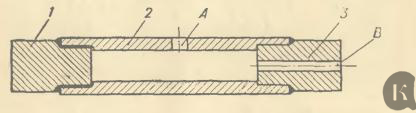
Фиг. 37. Пайка трубы с заглушками с технологическими отверстиями.
припоя и при вспенивании влаги (если флюс разведен на воде), а также для фиксирования положения втулки на трубе. Груз является также компенсатором температуры при пайке разностенных деталей и предохраняет тонкие детали от прогорания. Обычно этот груз изготовляется из стали; вес его и размеры подбираются опытным путем в процессе паяния.
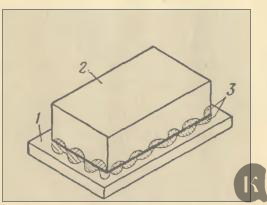
Фиг. 38. Положение флюса во время пайки.
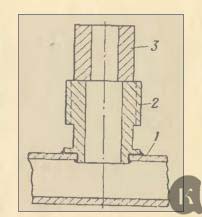
Фиг. 39. Пайка с компенсатором.
24. При пайке тонкостенных деталей с толщиной стенки до 2 мм (детали 1 и 2 на фиг. 40) при нагреве из-за неопытности паяльщика может произойти прожог тонкой стенки. От этого предохраняют фиксаторы-компенсаторы. Они же служат для фиксации втулки по отверстию трубы (правая сторона) и как оправка, предохраняющая от коробления стенки и фиксирующая диаметр, особенно, если отверстие изготовлено по 3-му классу точности. Компенсаторы могут быть различны по своей форме. Грузы-компенсаторы рекомендуется изготовлять для предохранения прожога деталей со стенками до двух мм. Это особенно важно, если детали с тонкой стенкой имеют толстую стенку основания.
25. В случае, показанном на фиг. 41, требуется припаять резьбовую втулку 2 к наружной стенке трубы 1. Втулка находится в своем -отверстии очень низко буртиком, так как резьба втулки расположена почти на одной поверхности с накладкой трубы (расстояние всего 2 мм).
Во время пайки этих деталей припой заходит на резьбу, что вы-
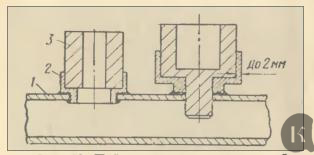
Фиг. 40. Пайка тонкостенных деталей с фиксатором-компенсатором.
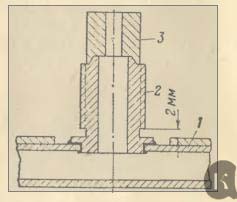
Фиг. 41. Пайка резьбовой втулки к наружной стенке трубы.
зывает впоследствии большие трудности — приходится калибровать резьбу после пайки.
При конструировании подобных узлов необходимо предусматривать, чтобы бортик втулки 2 находился бы на уровне верхней плоскости детали /, а не в углублении, как показано на фигуре.
В случае же, если конструкция выполнена так, как показано на фигуре, поступают следующим образом. Места образования шва зафлюсовывают как обычно, а резьбу втулки покрывают пастой из мела или графита или их смеси, замешенных на воде. Можно также изолировать резьбу смоченным водой асбестом, но этим способом паяльщики пользуются неохотно, так как во время нагревания некоторые нити асбеста загораются и горят очень ярким пламенем. Показанная на фигуре деталь 3 является компенсатором.
26. Близкое расположение мест пайки ведет к затруднению процесса пайки. Пайка узла, показанного на фиг. 42, производится следующим образом. Пластины 3 вставляются с двух сторон в пазы, которые имеются на трубе 1, и покрываются флюсом внутри трубы. Флюс наносится ровной полоской в местах образования шва. Чтобы пластины 3 не выпадали из своих мест, производят подогревание флюса до его стеклообразного состояния. Затем соединяют детали 2 и 1, покрывают их флюсом и устанавливают деталь 1 вертикально на детали 2. После этого- производят
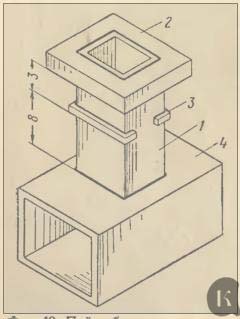
Фиг. 42. Пайка близко расположенных швов.
пайку детали 2; так как расстояния между швами спайки детали/с деталью 2 и детали 1 с деталью 3 всего 3 мм и температура в обоих швах одинакова, то припой одновременно забегает Б оба шва. Затем деталь 1 устанавливают на детали 4 и производят последнюю пайку узла.
Пайка близко расположенных швов (на расстоянии 3 мм и менее) одним припоем представляет собой очень большие трудности,
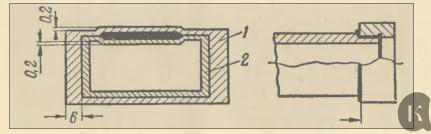
Фиг 43. Утяжки и выпучины от пайки.
так как при каждой отдельной пайке может быть распаян предыдущий шов. В таких случаях лучше всего производить ступенчатую пайку припоями с различными температурами плавления.
27. При соединении пайкой деталей 1 и 2 (фиг. 43), имеющих толщину стенок до 2 мм, может получиться выпучина до 0,2 мм, как
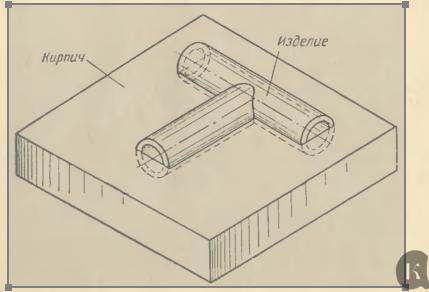
Фиг. 44. Простое приспособление для пайки.
указано на фигуре. Это происходит из-за неравномерности зазора, коробления, неравномерного прогрева во время пайки, неряшливой подгонки деталей друг к другу перед пайкой. Чтобы избежать выпу-чин, необходимо вставлять внутрь деталей оправки или скобки, чтобы внутренний контур остался правильным. Оправки должны быть пустотелыми и из того же материала, что и спаиваемые детали, чтобы избежать излишнего нагрева.
28. При пайке мелких деталей (фиг. 44) припоями, указанными в таблице, например, латунных трубок с толщиной стенки 0,5 мм
при наружном диаметре 6 мм, пользуются как приспособлением для пайки кирпичом. Для этого в огнеупорном кирпиче выдалбливают или высверливают наружный контур, который будет иметь деталь в собранном виде. Пайка указанных трубок производится горелками мелких номеров. Нужно предварительно нагреть детали в местах соединения, затем ввести в места пайки значительную порцию порошкообразного флюса (буры), который при расплавлении до стеклообразного состояния стягивает трубки, что обеспечивает плотное прилегание их друг к другу, а затем быстро вводить при нагреве небольшую порцию припоя. Такое приспособление просто и дешево и рекомендуется для мелкосерийного производства.
29. Пайка колец из ленты (фиг. 45) не представляет собой большой трудности, но требует внимательного и аккуратного исполнения.,
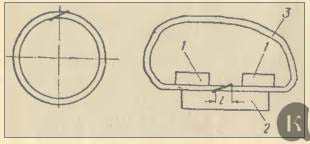
Фиг. 45. Пайка сепараторного кольца.
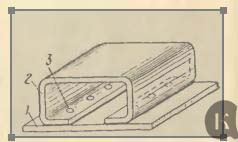
Фиг. 46. Соединение заклепками перед пайкой.
Длина развертки заготовки кольца отрезается в размер. При пайке паяльщик сгибает отрезок ленты, как показано на фигуре с правой стороны, устанавливает его на кирпич 2 и прижимает заготовку кольца 3 двумя грузами 1. На концах заготовки в местах соединения сделаны заранее скосы с каждой стороны на длину 1—7 мм Место шва покрываетс51 флюсом и производится пайка, а затем зачистка паяного шва, деталь 3 рихтуется на цилиндрической оправ ке и, если необходимо, производится механическая обработка. Таким же образом производится обработка специальных сепараторных колец, только отверстия по координатам для шариков обрабатываются и растачиваются в развертке.
30. При фиксации перед пайкой детали 2 на детали 1 (фиг. 46) можно избежать изготовления приспособлений для пайки. Лучше всего фиксацию производить заклепками из этого же материала. Клепку производить не окончательно, а с люфтом, чтобы припой смог проходить по всей плоскости. С введением заклепочных соединений появилась возможность перевести указанную деталь на пайку мягкими припоями вместо серебряного припоя.
31. Пайка контактов на многих производствах довольно трудоемка, так как обычно паять их приходится значительное количество, а мелкие размеры контактов и высокие требования к качеству пайки заставляют паяльщика быть особенно внимательным.
Контакт (фиг. 47) состоит из чашки 1, которая изготовляется из стали, и собственно контакта 2— вольфрамового или платинового. Для получения собранного контакта 3 нужно деталь 2 впаять в чаш-
ку 1. Для этого в чашечке 1 зафлюсовывают место припайки контакта и прогревают флюс, пока он не затвердеет. Когда мы наносим флюс внутри чашечки, надо следить за тем, чтобы он на 1 мм не доходил до отверстия е, иначе припой при нагреве будет скатываться в отверстие. Затем кладут в чашечку отрубленное кусачками маленькое зерно припоя и плавят его для того, чтобы припой расположился по краям чашки. После этого вставляют контакт 2 в чашку/и производят окончательный нагрев. Иногда при этом слегка нажимают на контакт, чтобы выдавить излишний припой.
Для того чтобы ускорить обработку контактов, делают простое приспособление 4 из латуни или стали на двадцать и больше гнезд
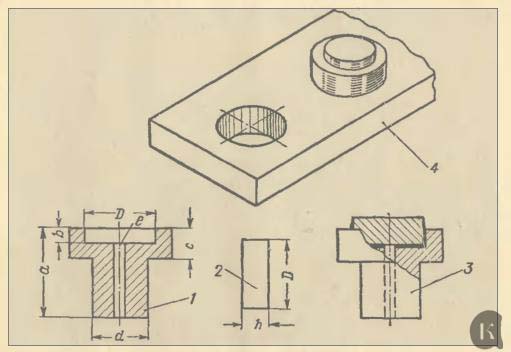
Фиг. 47. Пайка контактов.
с определенным шагом между отверстиями для контактов. После того как поставлены все контакты, работа производится по операциям, что намного увеличивает производительность труда паяльщика.
При пайке контактов иногда делают и так: листовой припой типа фольги разрезают на мелкие кусочки («глазки», как их называют паяльщики), место пайки покрывают флюсом и вкладывают глазок в гнездо контакта, а на припой сверху накладывают сам контакт; затем производят нагрев до расплавления припоя, и контакт Под действием собственной тяжести входит на свое место. Надо проследить за тем, чтобы контакт по всей поверхности вошел в гнездо До отказа. По окружности контакта должна выступить ровная полоска припоя. Пайка контактов с применением припоя в виде фольги наиболее эффективна.
32. Простое приспособление (фиг. 48) для пайки трубы с одним Коленом состоит из следующих деталей: корпуса 3, направляющих
стержней 4, 5 и 6 для фиксации трубы и колена. При установке в приспособление труба 1 одним концом надевается на неподвижный стержень 5, а другой ее конец фиксируется подвижным стержнем 4. Колено фиксируется стержнем 6 и закрепляется в приспособлении винтами. Нужно учитывать во время пайки расширение
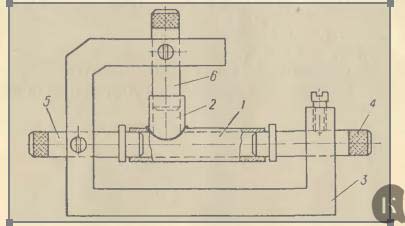
Фиг. 48. Пайка трубы под углом 90° на приспособлении.
латунных трубок от нагрева и направляющие стержни вплотную к трубам не прижимать. При пайке без приспособления отверстия труб получают овальную форму. Например, отверстие диаметром 13 мм после пайки имеет овальность 0,2 мм. При пайке с приспособлением овальности отверстий не получается. Рассмотренное
приспособление удобно при мелкосерийном производстве и дешево в изготовлении.
33. Требуется припаять (фиг. 49) к наружным стенкам трубы 2 втулки 1 и 3 и выдержать при этом после пайки
соосность отверстий между
втулками с точностью до
0,035 мм. Для пайки втулок изготовляется оправка 4, которая фиксируется на конус втулки/и цилиндрическую часть втулки 3 (допуск по 3-му классу
точности). Иногда (при больших диаметрах втулок) на торцах
втулок, соприкасающихся со стенками трубы 2, пропиливают надфилем канавки шириной 0,3 мм и глубиной 0,2 мм в форме треугольника. Это делается для того, чтобы был обеспечен проход припоя на торцы втулок. Места пайки втулок покрывают тонким слоем сильно измельченного флюса. Если слой Флюса больше необходимого, то во время пайки, когда мы прижмем втулку грузом, флюс может не выйти из-под торца втулок. Затем оправка 4 вставляется в коническое отверстие втулки 1 и закрепляется гайкой с шайбой. Полную затяжку втулки на конус производить не рекомендуется, а следует оставлять едва заметный люфт (это делается
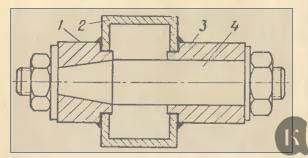
Фиг. 49. Соблюдение соосности отверстия во время пайки.
в связи с расширением металла во время нагрева). Затем с цилиндрической части оправки с заметным люфтом закрепляется гайка с шайбой. Порядок пайки следующий: деталь 2 помещают между двух кирпичей втулкой 3 вверх. Производится пайка втулки 3 к стенке трубы 2. Затем таким же образом производится пайка втулки 1. Как только процесс пайки закончен, необходимо без промедления отвернуть гайку со стороны втулки 1 и легким ударом, вынуть оправку. При пайке мы выдерживаем соосность между отверстиями втулок с точностью до 0,1 мм, так как после освобождения оправки 4 спаянный узел еще горячий и, остывая, коробится. Оставлять оправку до полного остывания нельзя, так как при остывании ее может зажать (латунные части остывают быстрее, чем стальная оправка). Чтобы выдержать установленную соосность с
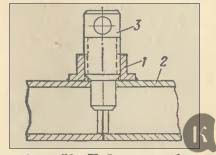
Фиг. 50. Пайка резьбовой втулки на оправке.
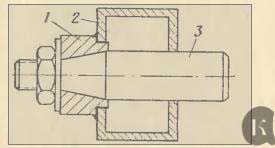
Фиг. 51. Пайка втулки на оправке с фиксацией на резьбу в другой детали.
точностью 0,0,35 мм, предусматривают механическую обработку шда специальную развертку. Рассмотренный случай требует большой квалификации паяльщика и соответствующей подготовки к выполняемой работе.
34. В узле, показанном на фиг. 50, требуется выдержать соосность при пайке между резьбовой частью втулки и отверстием трубы с точностью до 0,1 мм. Для изготовления узла с заданной точностью необходимо изготовить стальную оправку 3 с фиксацией на отверстие в трубе 2 и резьбовую часть втулки 1.
Необходимо предусмотреть, чтобы при механической обработке-соприкасающийся торец втулки 1 был изготовлен на базе резьбового отверстия. Перед пайкой втулка 1 надевается на оправку 3 и фиксируется в отверстие трубы 2. Конец резьбовой оправки и ее цилиндрическая часть иногда покрываются мелом, чтобы избежать возможного припаивания к втулке 1. Покрытия флюсом места пайки заранее производить не рекомендуется. В начале пайки прихватывают припоем с одной стороны втулку 1 к трубе 2 и еще горячей вывертывают оправку 3. После того, как мы освободились от оправки 3, пайку производят обычным порядком, предварительно положив на втулку 1 легкий груз (чтобы не допустить сдвига ее с места).
После пайки необходимо произвести калибровку резьбы во* втулке 1.
35. Панка (фиг. 51) втулки 1 с фиксацией на резьбовое отверстие противоположной стенки трубы не представляет большой труд-
пости. Аналогичный случай показан на фиг. 49 и 50. Разница лишь в том, что в рассматриваемом примере оправку 3 необходимо фиксировать на резьбовое отверстие. Соосность между коническим отверстием втулки I и резьбовой частью противоположной стенки трубы 2 можно выдержать с точностью 0,2 мм.
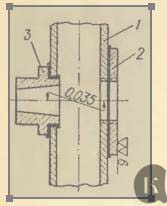
Фиг. 52. Технологические припуски для обработки после пайки.
36. В примере, показанном на фиг. 52, требуется припаять к наружным стенкам трубы 1 окончательно обработанную втулку 3 и накладку 2, которая должна обрабатываться по торцу с расточкой и нарезкой резьбы после пайки. В первую очередь мы производим припайку втулки 3 к трубе 1 (так же, как описано в 'примере, показанном на фиг. 36). Затем производим припайку накладки 2 к трубе 1. В накладке 2 и трубе 1 предусмотрено технологическое отверстие для фиксации их совместно на оправке при пайке (после пайки это технологическое отверстие растачивается до размеров заданного резьбового отверстия). После пайки необходимо зачистить торец втулки 3 с внутренней стороны трубы заподлицо со стенкой. После этого растачиваем отверстие и нарезаем резьбу с одновременной подрезкой торца под УУ 6 до нужного размера. Чтобы выдержать соосность с точностью 0,035 мм, расточку и нарезание резьбы производят на токарном станке с фиксацией на конической оправке с гайкой.
В случаях, подобных разобранному, механическую обработку резьбы и торца нужно производить после пайки. Выдержать соос-
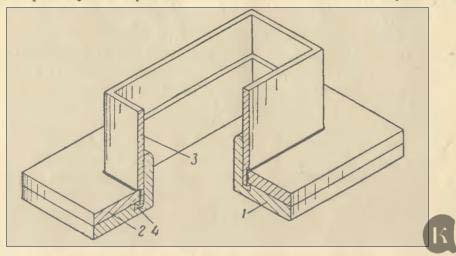
Фиг 53. Пайка трубы с фланцем на оправке.
ность 0,035 мм при пайке тонких стенок очень трудно и в таких случаях необходимо предусматривать технологические припуски, так как тонкие стенки конструкции сами по себе не обеспечивают этих допусков.
37. Часто требуется припаивать (фиг. 53) к трубе 3 фланец 2 так, чтобы они были взаимно перпендикулярны. Для этого изготовляют
простую пустотелую оправку 1. Труба 3 фиксируется на это приспособление своим внутренним контуром. На оправке I предусмотрены фаски 4 и канавки, которые перед пайкой покрывают мелом или графитом (или их смесью), чтобы во время пайки оправка не припаялась к приспособлению. Кроме того, оправка предохраняет внутренний контур трубы от коробления.
Если спаиваются труба и фланец больших размеров, то оправку применять не рекомендуется, так как в этом случае в месте спая получается раковичностъ. Тог-
да, чтобы избежать коробления, вместо оправки вставляется специальная латунная скоба.
38. Необходимо припаять (фиг. 54) трубу I с длинным (больше 300 мм) концом от радиуса изгиба к фланцу 2.
Нужно правильно установить трубу 1 и фланец 2 — обеспечить угол 9СР между осью трубы и осью фланца. Для этого применяется подставка 3.
На торец фланца должен давить груз 6, который прижимает фланец к подкладке и не
позволяет ему подыматься и коробиться во время пайки. Груз 6 не должен мешать паяльщику во время работы. Пластина 4 покоится на кирпичном основании 5. После пайки узел должен остывать вместе с подставкой и грузом, чтобы не было коробления. Если не
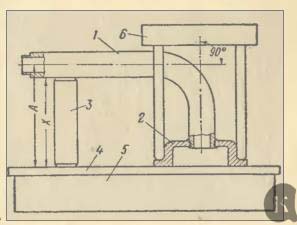
Фиг. 54. Пайка фланца с длинной трубой.
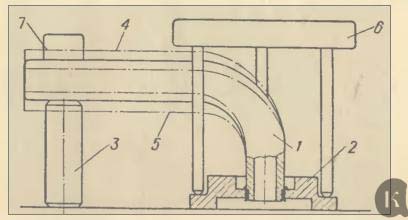
Фиг. 55. Исправление брака после пайки.
пользоваться описанными приспособлениями, труба 1 может принять неправильное положение, как показано пунктирными линиями 4 и 5 на фиг. 55. Обыкновенно такие ненормальности пайки не всегда можно исправить обычной слесарной рихтовкой. Выправить узел можно следующим образом. Нужно установить размерную оправку 3 и наложить груз 6 на фланец 2, а также наложить груз 7, который через трубу 1 опирается на подставку 3. Затем нагреваем
место пайки. За счет зазоров под пайку труба 1 займет правильное положение. После этого пропаиваем узел вторично.
39. В случае, изображенном на фиг. 56, требуется спаять детали 1,2,3 я 4. Для пайки необходимо изготовить простое приспособление в виде стального четырехмиллиметрового угольника 5. На угольнике расставлены шпильки 8 для фиксации детали во время пайки. Шпильки рассчитаны так, чтобы при расширении металла от нагревания они не упирались во фланцы и не оставляли на них вмятин.
Если труба 2 выходит за торец фланцев 1 и 3, то нужно сделать окошки-прорези в угольнике 5. Последовательность пайки следующая: производят сборку деталей 1, 2, 4 и 3, покрывают флюсом места соединения детали 2 с деталями 1 и 3; планка 4 устанавливается в вертикальное положение; устанавливается подставка 9 под трубу, предварительно рассчитанная по заданным размерам; затем производится припайка детали 3 к детали 2; после этого снимают оправку 9, перевертывают угольник 5 в нижнее положение для пайки детали 1. После спайки детали 1 с деталью 2 перевертывают угольник в первоначальное положение, деталь 4 устанавливается на подставки 7, которые заранее определены размерами чертежа для установки детали 4. На детали 4 перед пайкой устанавливается груз 6 (что предохраняет от коробления).
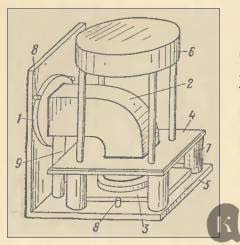
Фиг. 56. Пайка узла на приспособлении.
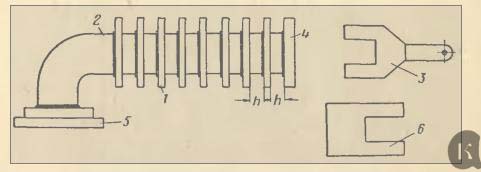
Фиг. 57. Пайка к трубе фланцев и пластин.
40. Необходимо припаять (фиг. 57) к трубе 2 фланцы 4 и 5 и также пластины 1 (8 штук) с размером между ними к. Пайка фланцев 4 и 5 к трубе 2 не отличается от описанной выше в подобных примерах. После припайки фланцев 4 и 5 все пластины для удобства пайки передвигаем к фланцу 5. В этом положении они удерживаются специально изготовленным для этой цели крючком из жести. Труба 2 устанавливается в вертикальное положение. Чтобы избежать разметки места каждой пластины на трубе 2 и не затруднять
паяльщика установкой их на расстояние к друг от друга, изготовляется простое приспособление 3 в виде вилки. Перед пайкой вилка 3 кладется на торец фланца 4, сверху опускается пластина для пайки, на шайбу накладывается дополнительно компенсатор 6 из стали или чугуна — так, чтобы остался свободный проход для удобства пайки. После этого производится пайка пластины. Затем компенсатор и вилка переставляются для пайки следующей пластины и т. д. Плоскость вилки 3, которая соприкасается с шайбами, должна быть покрыта мелом или графитом (или их смесью). Эти простые оправки намного увеличивают производительность труда паяльщика.
41. Требуется спаять (ф.иг. 58) детали 2, 3 и 5. В1 первую очередь производят пайку деталей 2 и 3 на приспособлении, как указано на фиг. 53. Затем производится подготовка к пайке уже спаянного узла с деталью 5 — устанавливается оправка 1 на технологическое отверстие в цилиндре 5.
Чтобы деталь 2 не припаялась к оправке, на оправке 1 сделаны в местах пайки фаски 4 (3X45°), а плоскости оправки 1, соприкасающиеся с деталью 5, и фаски на оправке покрываются мелом, графитом или их смесью. Нагревают в первую очередь массивные места детали 5. Отверстие диаметром О в цилиндре расточено предварительно, а после пайки оно' обрабатывается по 3-му классу точности. При пайке нескольких патрубков угол между их осями можно выдержать с точностью -Ц5'.
Если припаивать к цилиндру два или несколько патрубков, то даже при сравнительно толстых стенках цилиндра все же получается коробление. Поэтому при точных работах необходимо отверстие и наружный диаметр цилиндра изготовлять с припуском под окончательную обработку после пайки.
42. Требуется припаять (фиг. 59) трубы /, 2 и 3 к пластине 4. Нужно выбрать базы для фиксации труб во время пайки. В трубах /, 2 и 3 и пластине 4 после пайки должны быть расточены отверстия по 3-му классу точности, которые по координатам связаны между собой по 4-му и 5-му классам точности. Чтобы правильно собрать и спаять трубы и пластину, на месте будущих отверстий сделаны четыре технологических отверстия диаметром 4А4 в пластине и в одной стенке в трубах. Предусмотрены также технологические припуски по 2 мм на каждую сторону в пластине 4, которые после окончательной пайки обрабатываются механическим путем заподлицо с трубами 1 и 3. Эти технологические припуски нужны для того, чтобы припой во время пайки не скатывался.
Для фиксации во время пайки всех деталей было изготовлено простое приспособление 5, которое копировало по наружному кон-
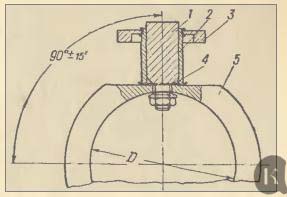
Фиг 58. Пайка трубы с фланцем к цилиндру на приспособлении.
туру форму пластины 4. На этом приспособлении были изготовлены четыре фиксатора диаметром 4С4. Перед пайкой на этом приспособлении необходимо подогнать зазоры для пайки между местами соединения в трубах с таким расчетом, чтобы учесть линейное расширение металла при нагревании. Необходимо также просверлить несколько технологических отверстий в приспособлении 5 и в пластине 4 в местах, которые соответствуют соединениям труб между собой, для того чтобы во время пайки не образовывалось воздушных мешков. Если этого не сделать, то припой на всю глубину не прой-
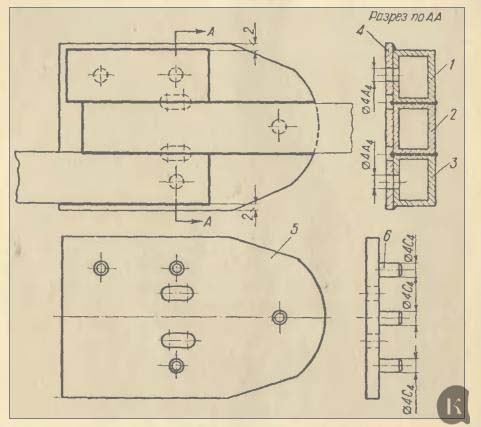
Фиг. 59. Сложная пайка труб к пластине.
дет, а стенки труб должны быть спаяны на всей длине и глубине соединения. Вначале необходимо припаять (прихватить) в шести точках, для того чтобы зафиксировать окончательное положение труб на пластине. После этого пайка производится в обычном порядке. Во время пайки необходимо наблюдать за тем, чтобы нагрев всех деталей был равномерным, так как в противном случае может получиться кривизна (выпуклость и вогнутость до 0,2 мм на длине 100 мм). После пайки в рассмотренном примере нужно произвести травление, зачистку мест пайки, рихтовку на разжимных стальных клиновых оправках или оправках по внутреннему контуру из фибры, текстолита или дельта-древесины.
43. Необходимо впаять (фиг. 60) в пазы трубы 1 пластины 2. Пластины 2 необходимо подобрать так, чтобы между пластиной и стенками трубы (с обеих сторон) оставался зазор. Пластины долж-36
ны выходить за контур трубы не менее чем по 1 мм на сторону. Это необходимо для того, чтобы с каждой стороны пластины можно было положить по кусочку припоя и припой не перекатывался бы на одну сторону. Иначе припой при расплавлении сосредоточится в одном месте и заполнит зазоры неравномерно.
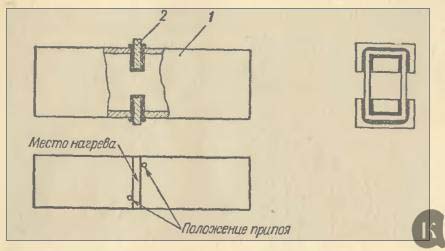
Фиг. 60. Пайка тонких пластин к трубе.
При подготовке к пайке необходимо: вставив пластинку в пазы, покрыть их флюсом с наружной части трубы и, держа деталь пассатижами в руках, подогреть флюс до его затвердевания. Как только флюс затвердеет, он будет удерживать пластины от выпадания и смещения из своих гнезд. После остывания детали необходимо произвести зафлюсовку (уже внутри трубы) стенок трубы и пластины. Флюс внутри трубы на пластине 2 в местах соединения с трубой 1 накладывать очень осторожно ровной полоской шириной не более 1 мм, так как по условиям изготовления детали разрешается выход припоя внутрь пластин фаской шириной не более 1 мм.
Нагрев производится в средней части пластины 2, для того чтобы припой расплавлялся одновременно и заполнял зазоры с каждой стороны равномерно, не прижимая пластину к какой-либо одной стороне. После пайки деталь поступает на дальнейшую обработку — для запиловки технологического припуска заподлицо с наружным контуром.
44. Необходимо припаять (фиг. 61) к наружной стенке трубы 1 втулку 2 и крышку 3. Для удобства пайки лучше всего начинать пайку с детали 2. Перед пайкой места спая на втулке и в отверстии трубы покрываются флюсом.
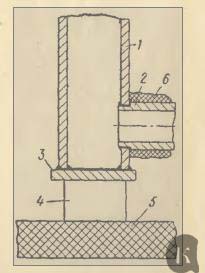
var container = document.getElementById('nativeroll_video_cont'); if (container) { var parent = container.parentElement; if (parent) { const wrapper = document.createElement('div'); wrapper.classList.add('js-teasers-wrapper'); parent.insertBefore(wrapper, container.nextSibling); } }